To define the problem, the field solver employs various numerical, approximating, and empirical elements in all simulation models. Steady-state Thermal Analysis (SSTA) models the material’s response to atmospheric pressure over time, while Transient Thermal Analysis (TTA) trajectories are scaled from a particular point in time.
Understanding transient thermal analysis and steady-state seems unnecessarily daunting to new engineers as fewer tutorials explain it effectively. Let us explore.
What is Steady-State and Transient Thermal Analysis?
Steady-state thermal analysis is a process used to determine the temperature distribution of an object in time. This thermal analysis is typically used to study the thermal properties of a material over time.
Transient thermal analysis, on the other hand, is a process that looks at how an object’s temperature changes with time. This thermal analysis typically studies how an object’s temperature changes as it heats up or cools down.
In transient thermal analysis, the component’s temperature is allowed to change. In steady-state thermal analysis, the temperature of the element is held constant. The transient thermal analysis is primarily used for dynamic events like a crash event or an engine start-up event. Steady-state thermal analysis is used for steady-state events like a car sitting in traffic or a cooling system at idle.
A Few Words on Finite Element Analysis
The Finite Element Analysis (FEA) is a numerical technique for finding approximate solutions to partial differential equations. This technique can be used in many areas of engineering and science, including the oil and gas industry, mechanical, aerospace, civil, chemical, and biomedical engineering.
The main idea behind FEA is to break down the problem into smaller, more manageable pieces. The smaller pieces are then solved individually, and the results are combined to get the desired solution.
FEA Simulation Model
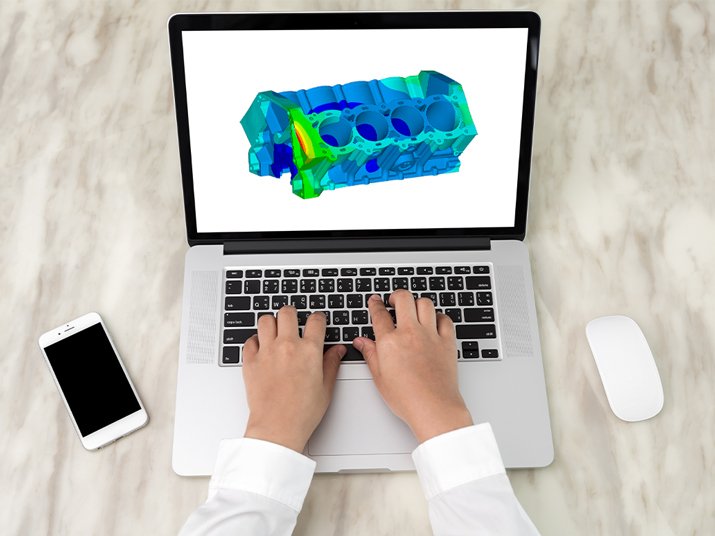
FEA Simulation Model simulates a product or structure and predicts how it will behave when it is subjected to a load, such as an impact, or when it is subjected to an environment, such as water or heat. It can also predict how a structure will behave when it changes, such as by adding new structures or alterations made to existing structures.
Steady-State and Transient Analysis for FEA Simulation Models
The two techniques are often used for simulation models and can be combined in various ways, depending on what data you need to obtain from your model.
Steady-state analysis is used to:
1. Provide a steady-state response to the input
2. Determine the steady state output after a transient analysis
Transient analysis is used to:
1. Indicate the response of a system during a transient event (input change)
2. Estimate how long it will take for the inputs to reach their new steady state value
3. Avoid the need for a steady-state analysis by “simulating” a transient analysis
The Steady-State Analysis is a simulation model that is typically used for the analysis of structures that have a constant loading. The Transient Analysis is a simulation model usually used to analyze structures with varying loads.
The Transient Analysis can be used to simulate the effects of sudden load changes such as shock waves, explosions, and earthquakes. It can also simulate dynamic events such as impact or vibration excitations.
Benefits comparison — Steady-State vs Transient Thermal Analysis for an FEA Model
The FEA software will allow you to set up steady-state and transient analysis models.
The steady-state analysis is a more straightforward type of FEA that does not consider the changing temperatures experienced by parts of an object over time. It can be used to analyze thermal properties independent of time or for studying steady-state conditions.
The Steady-State analysis is more advantageous in comparison to the Transient analysis. The transient analysis is much more time-consuming and requires much computational power, so it will take much longer to generate results.
The Steady-State analysis is also better for analyzing the thermal properties of parts or components that are not subject to temperature changes. This includes the thermal properties at different temperatures, such as heat and specific heat capacity. The transient model is a more accurate representation of heat transfer. This model includes the effects of convection, radiation, and conduction on the surroundings and objects experiencing heat transfer.
How do I do a Steady-State or a Transient Thermal Analysis?
Simulations tools allow you to set up your transient thermal analysis and simulate it with your desired parameters. It also provides a graph of temperature distribution and heat transfer coefficient versus time, which helps you determine when to stop the simulation if you are interested in a particular time.
What is the Best Simulation Method for Me?
The best simulation method for you depends on what you need to do with your model and how much time you want to spend to get an accurate result.
The simulation models that use transient thermal analysis are more computationally expensive than those that use steady state because they require more iterations and more complex solver algorithms to converge on an answer. Confused about simulation tools? Read more here.
Wrapping Up
Steady-State simulation initializes a temperature distribution and then monitors the steady-state change in temperature as time passes. Transient Thermal Analysis initializes a temperature distribution and tracks all changes in the system either due to heat generation or by force applied for a prescribed elapsed time until steady-state is attained.
A transient thermal analysis evaluates the amount of thermal load on the metal parts during work to better understand heating in machines and industrial processes such as baking, forging, or welding. Steady-State testing is usually performed to evaluate materials with high thermal mass and low thermal conductivity. As these materials rely on large currents of heat to achieve equilibrium between their core design characteristics (e.g., hardness or tensile strength) and their environment, designers need to know how they will react under a given set of operating conditions.
The difference between steady-state and transient analysis for FEA simulation models is the time duration. The steady-state analysis assumes a constant input or boundary condition, while transient analysis is dynamic, with inputs or boundary conditions that change over time.
Mechartes is here to Help
Leading CFD and FEA Simulation Provider, Mechartes has provided a wide range of engineering simulation solutions for more than 16 years. We provide the best service after completing more than 5000 projects in the past – unmatched performance and great feedback are available. Set up a meeting with our experts.