When building an FEA simulation model, it’s vital to have a clear vision of your model before you begin, regardless of your background with FEA, whether as a seasoned FEA analyst or a novice.
Starting without a solid view of the design is a surefire way to end up with unintentional design trouble. Or, at the very least, a design that offers questionable results and the wasted effort repairing and iterating the model, further setting you on a path to digging a deeper hole to solve said issues.
Things to consider before building FEA simulation model
While common sense would have you thinking about booting up your simulation tool and getting on with it, there are a couple of crucial things to consider before beginning to build your model. To successfully jump-start your process flow for venturing into building an FEA model, here are five things you should know before you begin.
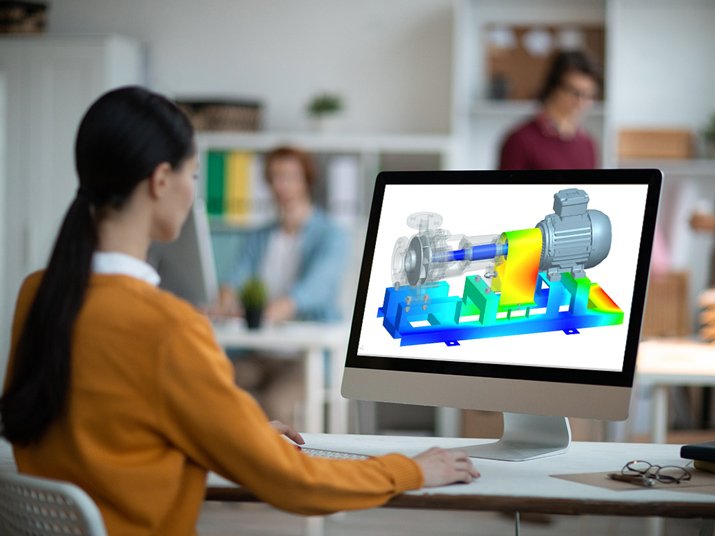
1. Define Your Problem
Outlining the problem is the first and foremost step to building a successful FEA model. Defining the issue allows you to understand it better and gives you a clear vision of formulating a solution. For example, let us assume that you are modeling a transmission shaft for an SUV; some of the areas that you need to focus on are
-
What is the torque curve of the engine?
-
What sort of gearing ratios would the shaft go through?
-
How much axial load would the shaft experience?
-
What are the transmission tunnel dimensions that the shaft has to fit?
-
What’s the operating weight that the bearings and chassy bear?
Formulating such questions would allow you to focus on defining the problem accurately, enabling you as a designer to make efficient decisions further down in the designing stage.
Also read: 10 Crucial Uses of CFD Simulation and Modeling
2. Choose the Type of Analysis
Modern FEA software has unlocked endless potential to conduct various forms of analyses such as structural, thermal, acoustic, electrical, and more. The question is, what’s best for your model? And how does it help you validate your solution concerning the problem?
Choosing the ideal type of analysis or a combination of analyses would empower you to test your designs extensively and in an area that matters the most. For instance, an automobile design would require an analysis of structural, thermal, aerodynamic, and material analysis to ensure that it meets the design requirements and offers optimum performance.
3. Mind the Materials
The composition of your model is just as important as the model itself when it comes to FEA. Depending upon the design and its use case, one material could be more suited than another. With FEA, you can play around with various materials putting them through realistic simulations that test the design in every conceivable manner.
You can also test your design with new materials or alloys that can further enhance its capacity and durability. Since the design is digitally simulated, you also have the choice of stress testing the design to understand its limits and estimate material, labor, and logistic costs.
Also read: What Are the Core Components of CFD Analysis Services in the Building Industry?
4. Engineer Your Model
Now that you have your basics, it is time to focus on the details. There is a high possibility of missing & messing up many design elements during preliminary design leading to problems during production and physical testing. It is also an ideal time to integrate your FEA design with other components of your design or environment to evaluate it entirely.
It’s now a great time to integrate your design, evaluate how it interacts with its overall design, and make any necessary adjustments if required. Often some auxiliary elements need to be designed to make the integration seamless. This step is also often overlooked by designers and leads to last-minute adjustments, which lead to further complications.
5. Output Essential Results
FEA sim result files are bloated with excessive pre-processors. While you may inherently choose to export and handle these files as they are, it is best practice to eliminate some pre-processors depending on your needs.
This step improves your ability to move, store, and process designs efficiently. This data, which can be recorded in tabulated form and stored in the Abaqus data (.dat) file, can include information on contact behavior as well as stresses, strains, displacements, and forces at particular nodes and elements of interest. We probably would not want to extract this data from the system after the fact manually.
Also read: What Are Different Methods of Using CFD Simulation for HVAC System Designing?
Consider Mechartés
FEA simulations have sparked a revolution in almost all sectors with their impressive RnD capacity. However, it is still a complex process with granular procedures that impact the results significantly. Suppose one decides to employ an FEA simulation model in any capacity. In that case, it is done best by skilled professionals to ensure the production of effective sims that accurately reflect one’s ideas.
This situation is where Mechartes steps in. With over 15 years of experience, 5000 completed projects, and an emphasis on producing reliable simulation results, Mechartés is a leading CFD & FEA business specializing in optimum engineering and process solutions to solve challenging engineering challenges.
Final Thoughts
This article aims to draw attention to some factors you should focus on before building an FEA simulation model. Though they may be simple, these steps are crucial to effectively identify, plan, construct and refine a design to meet your requirements.
Hopefully, these steps will aid you in developing effective FEA models in the future that are flawless and well executed. With these steps, you’ll be producing models on par with the best in no time!