FEA, or finite element analysis, is a computer-aided design and manufacturing technique that analyses a product using computational fluid dynamics. But sometimes, the design team and FEA modeling professionals don’t agree on the final product and have to go back to the drawing board.
FEA is a numerical method used to calculate the stress and strain states under arbitrary loading conditions. Designers can generate a model by solving partial differential equations that describe the forces that act on the system.
However, there are some reasons why your FEA Analysis won’t work. Let us discuss this.
How Does FEA Work, and What Is Its Importance?
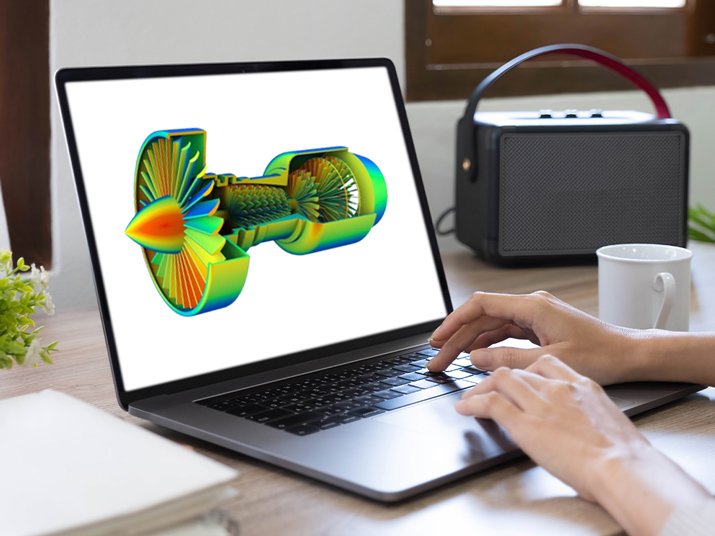
Designers use FEMs (Finite Element Methods) to approximate partial differential equations on systems of algebraic equations and boundary value problems with degree-of-freedom. Experts use algorithms such as the Lagrange-Galerkin Method to approximate ordinary differential equations.
Sometimes your simulations might not work, even if you’ve gone through all the steps and checked for errors.
Here are six reasons why your FEA Analysis doesn’t work.
1. You Don’t Know the Material Properties of Your Parts
The FEA process starts with identifying the type of simulation needed (static or dynamic). You must define the geometries of the analyzing part before any analysis can occur. Depending on the input method, you can use using drawings or dimensional data in digital form. Next comes choosing material properties from databases that contain properties for standard materials like aluminum, steel, titanium, composites, and plastics.
It’s imperative to consider the material properties of your parts or assembly when designing your FEA simulation, as it can make or break your design.
An excellent way to avoid this problem is to use an online tool like SimScale or ANSYS Workbench, which will automatically calculate your material properties based on what you put into the system.
2. You Are Not Using the Correct Solver for Your Model
You must use the correct solver for your model to get accurate results. If you are not using a suitable solver, your results may be inaccurate or wrong.
There are many different finite element analysis solvers and software available on the market today. It is crucial to choose the one that matches your needs and budget.
The finite element analysis solver you are using needs to match the problem you are solving:
1) The linear solver is best used when the materials used are linear-elastic with constant properties.
2) Nonlinear solver is best when your problem is a nonlinear material with constant properties
3) The generalized solver allows you to use general models of materials.
3. You Have Not Prepared Boundary Conditions Properly
Failure to account for friction in an FEA analysis can lead to inaccurate results. Luckily, there are other ways to correct the issue. Proper selection of boundary conditions, considering the effect of temperature on the results, and knowing how to select different types of materials are all critical factors when designing your FEA analysis.
This is a concern that many people have when they are using finite element analysis software. The accuracy of the results depends on the boundary conditions applied to the model.
Boundary conditions are essential for any analysis because they can change the outcome of the simulation. They describe the physical properties of the analyzing material and may also specify how other parts of the system interact with it. Choosing the appropriate boundary conditions for a given application is paramount.
4. The Mesh is of Poor Quality and Doesn’t Refine Enough
With finite element analysis software, it is possible to get a more accurate representation of the material properties of a product.
However, it can be challenging to use this tool correctly as the mesh quality is often poor and doesn’t refine enough.
The mesh is the set of all points on a surface that are connected by boundary surfaces. You can refine a mesh by increasing the number of boundary surfaces and their shape, size, and orientation. You must refine the mesh enough to provide accurate results for finite element analysis.
5. Your Model Is Too Complex for Your Data Set
To make finite element analysis software work for your data set, you must identify the type of data you are working with. If the data is continuous and not discrete, linear regression is the best option. Logistic regression is best suited if the data is discrete.
The second step to building a model is understanding what the model should output and what input variables it should take. For example, binary classification would be appropriate if your model will have continuous or discrete outputs but not both simultaneously.
In cases where a model can’t predict the outcomes simultaneously and have both types of outputs or inputs, a multinomial logistic regression might be more suitable. This will allow to predict multiple independent binary and continuous variables simultaneously.
6. You Are Using the Wrong Approach to Solve the Problem
Using FEA tools without the proper approach may not always be the most efficient way to solve problems in creative industries like design or architecture. However, there are ways that you can use these tools creatively to generate new ideas and solutions for design problems.
Are you confused about the approaches? Talk to one of our FEA geniuses now.
How to Make Your FEA Analysis Work?
FEA is a handy tool for engineers and manufacturing professionals. It allows them to analyze and predict the mechanical properties of different materials. Many factors can make it difficult for you to use FEA software to its full potential.
First, you must ensure that all the components and materials are listed correctly to identify any errors. You also need to ensure that you set all the parameters correctly and that all the data is accurate.
The next thing you need to do is check if all the assumptions are correct and if they are within your design specifications. There will often be an assumption or two that will be incorrect, leading to errors in your results.
Mechartés is Here to Help
Mechartés offers professional simulation results with an engineering approach. With accurate and reliable simulations, cutting-edge methodologies and simulation algorithms, large computer capacity, etc., you can rest easy knowing the result is likely to be highly accurate.
Reach out to us to learn more.