CFD Simulations and FEA Analysis allow engineers to design well-engineered and optimized designs before utilizing resources for prototyping and testing. These simulations would not serve their purpose without accurate models created with Meshing.
Meshing is the process of converting a continuous object, which contains infinite degrees of freedom into several smaller and discrete elements with well-defined degrees of freedom to perform simulations.
Here is everything you need to know about meshing and its importance for structural FEA and Fluid CFD:
The Fundamental Difference Between FEA and CFD
A Finite Element Analysis (FEA) is used for a simulation to analyze the mechanical properties of the component. In addition, Computational Fluid Dynamics simulations are used to analyze the fluid or flow properties of the component.
FEA simulations usually involve analyses of the mechanical properties, thermal properties, vibrational properties, etc. On the other hand, CFD simulations involve analysis of properties of heat and mass transfer, flow reactions, fluid dynamics, etc.
Meshing for both FEA and CFD is a similar function. A complex geometric structure is discretized into cells during meshing and has distinct nodes. The cells can be shaped accurately to capture the object’s physical shape by taking predictable shapes.
Importance of Meshing in FEA and CFD
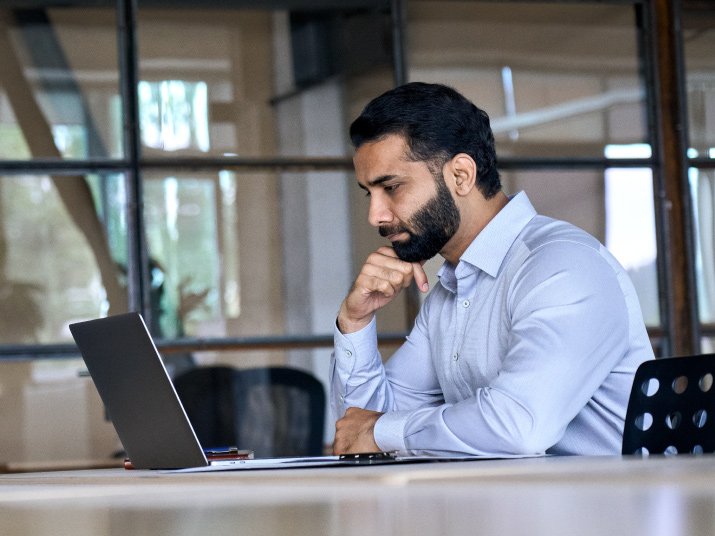
Meshing plays a critical role in the simulation process. A high-quality mesh ensures accurate simulation results. The quality of the mesh defines the accuracy, convergence, and speed of the simulation.
The meshing process is usually the most time-consuming part of the simulation process, as it involves very intricate processes that could significantly affect the accuracy of the simulations.
The meshing process becomes more critical and complex when the design involves complex geometries. Meshing allows for the complex structures in a component design to be solved based on several basic structures and combining these solutions. Meshing is done based on the nature of the simulation and the kind of forces that influence the component function.
Meshing in Structural FEA: Best Practices
These general guidelines help to create accurate meshes for FEA Analysis:
Mesh density
A finer mesh produces more accurate results. This is because the more minor elements in the mesh help capture the gradients across the shape more accurately and easily. However, adding more elements to the mesh can increase costs computationally.
When more elements are added to the mesh, more equations are being solved, increasing solution time and memory needs. The results from the analyses can also take more disk space.
These additional costs can be reduced by restricting high mesh density to the areas of interest only, which is sometimes the load path of the model with significant stress levels.
Convergence and stress singularities
A convergence study can be helpful when meshing for both FEA and CFD. After the simulation, the results are converged and then used in meshing, which reduces the mesh size.
This, however, does not have any effect on the results. This can help increase the mesh’s accuracy based on convergence studies.
Element shape and quality
Hexagonal and tetrahedral element shapes are the most used in structural analysis. Sometimes, pyramid and wedge-shaped elements exist but only as transitional between hex and tet element shapes.
The geometry represented in the analysis determines the element shape that is to be used for meshing. In the case of highly complex geometry, tet elements are used. The geometry is divided into smaller parts before using hex elements. But, this increases the time of analysis.
However, tet elements tend to be less efficient as more tet elements need to be used in place of hex elements to represent the same geometry.
Meshing in Fluid CFD: Best Practices
Here are some practices that can help create high-quality meshes for CFD simulation:
Geometry wrapping for watertight fluid models
Often design engineers use geometries that are hard to import into the fluids modeling programs. These gaps and leaks in the geometry take hours or days to fix.
Hence, using CFD software can effectively wrap the surface mesh around the discontinuous geometry. The automated geometry will fill the gaps, allowing more simulation and results analysis time.
Overlapping geometry for flow boundary
Inverse fluid volume is needed when performing a fluid analysis. This is achieved by wrapping a box around watertight geometry and combining the overlapped faces between the solids into one face. This removes the intersections between the box and the source geometry. The volume can be later extracted and imported into the fluid models.
Connecting meshes conformally
Using fluid models with a coarse mesh for large areas and fine meshes for detailed geometries reduces the computational time.
However, there may be a challenge linking these disparate meshes into a continuous mesh or reducing the accuracy by creating non-conformal mesh interfaces.
Linking meshes conformally can be a tedious job as it requires cleaning the geometry and manually correcting the meshes to fit everything nicely.
High-Quality Mesh with Mechartes CFD Simulation Experts
Building a high-quality mesh that can produce accurate results is a job for a simulation expert. However, the combined expertise and industry knowledge of simulation experts and engineering design teams at Mechartes can create the best meshes based on the project requirements and needs.
This not only helps to produce accurate results but also helps maximize efficiency and increase the design’s success rate. Our expert teams can leverage the right technology for your design project and create a fail-proof mesh of complex geometry using best practices for Structural FEA and Fluid CFD Simulations.