Specific techniques for machine condition monitoring and diagnostics are used widely in almost every industry, with automation, predictive maintenance, and quality control applications. Mechanical vibration analysis is one of the most commonly employed techniques used for this purpose.
Various methods for processing vibration signals have been proposed and proved effective in condition monitoring and diagnostics of different kinds of machinery.
In the case of the vibration-based condition, monitoring of rotating machines with multiple bearing systems, such as turbo-generator sets, is data intensive. Since several sensors are required at each bearing location, diagnosing faults on these systems may be daunting and requires judgment and expertise from a trained analyst.
Let us explore some more details about mechanical vibration analysis, its application, and its benefits.
What is Mechanical Vibration Analysis?
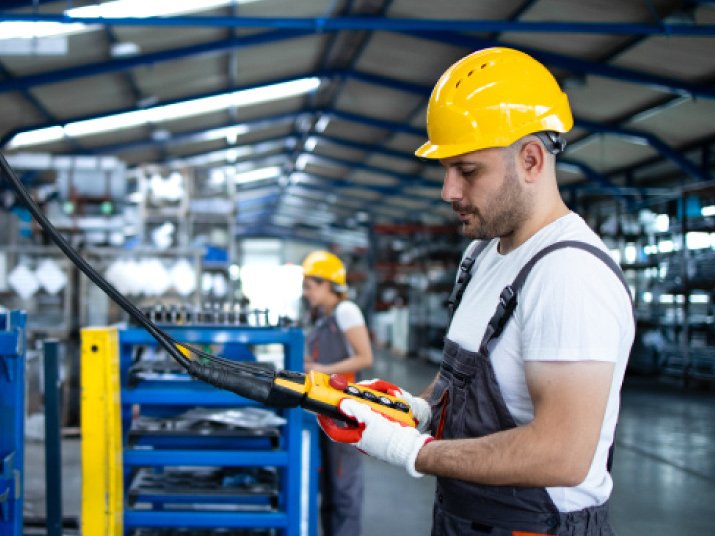
Mechanical vibration analysis is a solid technique for fault diagnosis of rotating machines. It involves monitoring the extent to which the different components of a machine vibrate during operation.
Vibration analysis helps identify the wear and tear of rotating machines with multiple bearings, say a multi-stage turbo-generator set.
Mechanical vibration analysis uses many vibration sensors and requires measurements from each bearing location, which results in the acquisition of large volumes of data. Hence, it is a relatively complicated process that mandates judgment and expertise from a trained analyst.
Techniques for Processing Vibration Signals
Signal processing aims to extract and display the maximum amount of helpful information from the measured data that best represents the health of the machinery to make diagnosis much easier for the user.
1. Fast Fourier Transform Technique
The fast Fourier transform is the most widely applied signal processing technique. The output of the fast Fourier transform is represented in the amplitude of the Fourier spectrum for feature extraction and analysis. This signal analysis technique is a powerful method based on the spectral approach for diagnosing various vibration-related problems in rotating machinery.
Although the fast Fourier transform technique proves a powerful diagnostic tool in stationary conditions, they fail to do so in several practical cases involving non-stationary data. The failure could result either from fast operational requirements, such as the rapid start-up of an electrical motor, or from the presence of a fault causing a discontinuity in the vibration signal being monitored.
Standard techniques used to analyze casing vibration are effective for health assessment but cannot give diagnostic information. In addition, these techniques globally characterize the vibrations over the whole machine cycle, while vibrations in cam mechanisms are highly non-stationary. Thus, these standard techniques may not be highly sensitive to faults in the early stage of development.
2. Wavelet Transform Technique
Regarding non-stationary effects in machinery vibrations, these may be very important, particularly in certain kinds of machinery, such as reciprocating machinery, in which different dynamic phenomena occur in different phases of the machine cycle.
Moreover, faults often produce dynamic effects only in correspondence with specific instants in the cycle. However, most of the widely used processing techniques analyzing vibrations in the amplitude or frequency domains are based on the assumption of stationarity and globally characterized signals thus. They are only partially suitable for detecting short-duration dynamic phenomena, whose time localization and identification are also impossible.
Time-frequency methods like wavelet transform tools are used to mitigate this situation. They are applied to a vibration monitoring system to accurately detect and localize faults occurring in the system. The wavelet transform is one of the new and powerful tools in the critical field of structural health monitoring using mechanical vibration analysis.
They are mathematical tools adopted for processing transient signals in different areas of vibrational analysis. The wavelet analysis reveals how the vibration frequency content varies within the machine cycle. Consequently, it makes it possible for transient dynamic phenomena to be clearly detected and precisely localized.
Importance of Mechanical Vibration Analysis
Rotating machines cover a wide range of critical facilities and provide the backbone of numerous industries, from gas turbines used in the production of electricity to turbo-machinery utilized to generate power in the aerospace industry.
These machines must run safely over time and under different operational conditions to ensure productivity and prevent any catastrophic failure, which would lead to costly repairs and may also endanger the lives of the operating personnel.
Areas of application of rotating machinery in everyday life and for industrial purposes like automobile, oil & gas refinery, etc., has increased tremendously with the industrial revolution. For all these rotating pieces of machinery, the faults introduced due to fatigue play a significant role in their failure. Overall, catastrophic failure is a big problem to solve.
Under the various maintenance techniques, mechanical vibration analysis is widely used to assess the rotating machinery’s health condition. The bearing faults induced in rotating machinery can be investigated experimentally using automated vibration analysis techniques.
In a rotating machine, the rolling element bearings are commonly subjected to unbalanced forces, leading to different types of faults in the rolling element bearings. The unbalanced forces simultaneously lead to the rotating machinery’s failure, and the bearing faults cause various problems leading to improper functioning of the rotating machinery.
Problems may arise for multiple reasons, including the contemporary presence of different vibration sources and noise, the presence of non-stationary dynamic phenomena, and the influence of the transfer functions between vibration sources and transducers.
Hence, developing advanced signal processing techniques and selecting the most effective ones for each kind of monitoring and diagnostic application is eminent for mechanical vibration analysis. It helps determine the factors that can ultimately lead to the failure of the machine.
Key Takeaway
The results from our mechanical vibration analysis are used to identify the wear and tear of the moving parts of machinery used across various industrial applications. In addition, sophisticated signal processing techniques provide the performance analysis of machines that help in their predictive maintenance and quality control.
The results from our mechanical vibration analysis can evaluate the problem areas and help in improving the overall health and safety of your equipment.
Mechartés carries out mechanical vibration analysis of machinery across various industrial domains. Our objective is to extract and display from the measured data the maximum amount of helpful information with utmost accuracy that best represents the health of the machinery to make diagnosis much easier for the user. Furthermore, The dedicated and skilled analysts at Mechartés can process large amounts of data with precision and accuracy.
Contact our service advisor for more details.