Developed in the 60s and perfected in the 80s, Computational Fluid Dynamics (CFD) has come a long way since its inception; the complex programming, calculation, and exceedingly long render hours are gone. Instead, modern CFD tools allow designers to seamlessly design new products and implement changes.
CFD has become an invaluable tool to designers and manufacturers across almost all sectors. It serves as a critical tool to help designers and manufacturers understand the behavior of a particular design in dealing with air, pressure, and fluid flows through virtual simulation. CFD has also evolved over the years to become a more robust tool that delivers accurate simulations in a short time.
Sounds good, right? The benefits don’t end there; in this piece, we’ll explore why CFD is an excellent tool that needs to be a part of every Turbomachinery Parts by Manufacturers’ process flow.
Check out our guide to optimizing CPU cooling systems here.
Why Should Manufacturers Consider CFD?
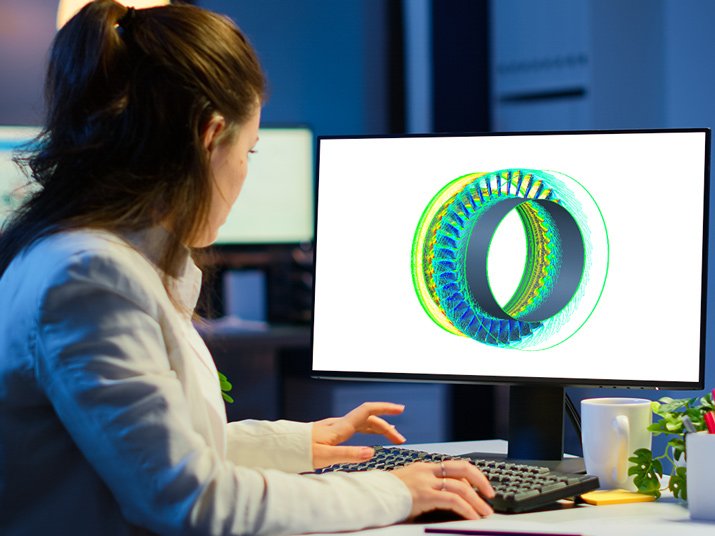
CFD is a godsend for modern designers and manufacturers as the increase in product complexity coupled with various constraints has made the manufacturing process infinitely more complex.
Along with structural simulation, designers now need to look into other analyses to ensure the product meets all requirements. This situation is where CFD comes in.
CFD dissects the interactions and flow of fluids of a given model, including both liquids and gasses, and can investigate natural phenomena such as pressure, temperature, and airflow.
As a result, CFD can help you avoid some of the most granular problems during product development and avoid failure. It’s also advantageous that it aids manufacturers cut down on time and cost of production during the development and production cycle.
Understand CFD like a pro by following this link.
Benefits of Implementing Computational Fluid Dynamics for Manufacturers
CFD has revolutionized the way parts are designed and manufactured. It allows designers to visualize and test their designs before manufacturing a prototype.
Here’s why turbomachinery parts manufacturers should seriously consider CFD:
Computational Fluid Dynamics saves time and eliminates prototyping
Unlike the conventional approach to design and prototyping, the CFD approach cuts down on the time and cost required for building a fully functioning product.
In addition, with CFD, you can confidently skip the prototyping phase as you will be able to test your design in the software environment to check if it meets your design requirements.
Stress test for extraordinary conditions
Turbomachinery often comes under a lot of stress and strain during operation, and it’s essential to check the tolerance for safe operation.
CFD allows designers to put the design through extreme conditions to understand how their design behaves in various situations and loads. CFD approach makes it much safer to test the turbomachines in extreme conditions and doesn’t cost as much.
Streamline your research and development process
Navier-Stokes calculations are often complex and time-consuming to ideally identify and implement. Without a proper value to work with, the efficiency of the design can take a huge hit.
However, with the CFD tool, the Navier-Stokes calculation can be fine-tuned to perfection and save valuable time and effort.
Eliminating design hazards
CFD also allows designers and manufacturers to reduce design hazards and improve operator safety. Designers can also simulate use cases to optimize their designs without compromising operability and compliance with safety regulations.
A wider variety of applications
CFD has a wide band of applications that can help you design and test anything from HVAC systems to turbomachinery parts to aerodynamic and water flows.
So it is a multifaceted tool that will revolutionize your design and R&D approach for the better in the long run.
Check out five ways to improve your CFD design’s accuracy here.
In Essence
The Computational Fluid Dynamics approach for turbomachinery parts is an ideal way to aid the designers and manufacturers in designing and producing products of high efficiency and complying with all safety standards. CFD also cuts down significantly on R&D and testing costs while keeping the process within a short timeframe.
As turbomachinery equipment is a costly and complex mechanism that handles high pressure, voltage, and temperature conditions, it’s necessary to ascertain the design’s safety, performance, operating range, and costs to ensure success.
Taking up the Computational Fluid Dynamics process-flow delivers on all these aspects with the overall optimized operation, which otherwise would compromise one of these factors.
Mechartes is home to highly skilled CFD experts who employ robust technology and techniques to conduct CFD simulations that meet and exceed your requirements. Our proven methods enable manufacturers to design and visualize products to the T.
Reach out to us today and learn more about our CFD Simulation and validation services and how we can help your business.