Manufacturing industries cannot ignore hydrostatic pressure testing as stringent governmental regulations ensure the non-negotiable quality of products. In the case of meter skids, pipelines, and compressed gas cylinders, hydrostatic testing is the technique of choice for determining whether or not there are leaks and evaluating the structural integrity of the components.
Hydro-static pressure will also impact fatigue loads in pipelines subjected to live loads such as vehicle loads and population distribution. So, with all these impacts on structurally stressed concrete structures, engineers face more challenges and pressure than ever before!
Let’s look at hydro-static pressure simulation from an engineering or Finite Element Analysis consultants’ point of view. How is it modeled, and why does it matter?
How Finite Element Analysis Consultants Meassure Hydro-Static Pressure
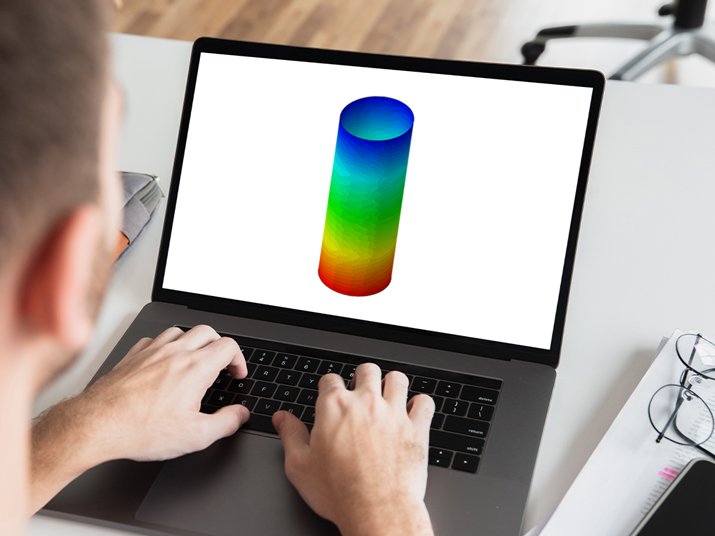
Designers can calculate hydrostatic pressure by using Pascal’s principle. Pascal’s principle states that when a fluid is at rest and confined between two flat plates, the pressure exerted on each plate will be equal in magnitude but opposite in direction.
Hydrostatic pressure is also known as “gauge pressure” and increases as you go deeper into the water column.
Hydro-static pressure is the pressure exerted by a fluid at rest on the walls of its container. It is calculated by multiplying the density of the fluid (ρ), acceleration due to gravity (g), and the height (h) of water above that point. Hydro-static pressure is essential in many engineering applications, including structural design and analysis.
How is Hydrostatic Pressure Simulated Using FEA Modeling?
Hydrostatic pressure simulation is used for fluid-structure interaction analysis to predict the pressure distribution inside a fluid-filled system.
It is usually done by solving equations of motion for the fluid and equations of equilibrium for the solid. Hydro-static pressure simulation can be done using FEA simulations.
This is shown by the ability to predict the pressure gradient of a liquid-filled tank from the bottom to the top without having to model the fluid. Let us discuss implementing hydro-static pressure in finite element analysis (FEA).
The first step in hydrostatic pressure simulation is to apply the hydrostatic pressure to the surface of an object. Engineers can do this by using a set of boundary conditions or an applied load on each face or node within the model.
The second step in hydro-static pressure simulation is calculating how this affects different surfaces within the model, such as walls, floors, and ceilings. Designers can do this by solving equations for fluid-structure interaction analysis (FSI).
Estimating hydrostatic bearing load has many challenges that often appear in highly viscous oils or steam reservoirs and complex geometry models. But Finite Element Analysis consultants come to the rescue with their algorithms for solving these problems.
Hydrostatic pressure is something that an FEA simulation can accurately model and predict. It provides engineers and Finite Element Analysis consultants with a detailed roadmap for manufacturability and leak testing. It considers real-world physics, such as fluid dynamics, shear forces, heat transfer, structural integrity, etc., to explain how fluids behave in concrete structures. This affects the leakage risks and maintenance costs in the long run.
Why is Hydrostatic Pressure Important for Designers?
Designers and engineers must consider hydrostatic pressure when designing and optimizing pipes, bridges, tunnels, and other structures. They must ensure that the structures are not only able to withstand the weight of water but also be able to withstand any external forces as well.
Fluids exert pressure on a shell’s surface by penetrating it and pushing it outwards. The hydrostatic pressure model is used in finite element analysis to represent fluid loads on shells caused by internal pressure. It is a straightforward and reliable method for analyzing shells under internal hydrostatic pressure.
Regardless of the form that the container, tank, or building takes, you may use this strategy successfully. However, depending on the material being analyzed or the density of the liquid being stored, you may employ a different approach. Examples might include pressure vessels and tanks for storing liquids such as water or oil.
In addition, the model must have the appropriate orientation for the loading to be accurate.
The hydro-static pressure modeling approach is widely regarded as a very trustworthy technique for modeling the behavior of liquids and has been exhaustively confirmed by field testing.
FEA Models and Software for Hydrostatic Pressure Analysis
FEA simulations and software for hydrostatic pressure analysis are used in many industries. Engineers and finite element analysis consultants use the FEA simulation models and software for hydro-static pressure analysis, which are also used in the design process to verify the performance of hydraulic systems before they are built.
Hydro-static modeling is a very complex and time-consuming process. The software used for hydraulic modeling can make the entire process easier and faster. Many types of software are available in the market, but they are not all equally good.
When buildings, tanks, vessels, or containers are exposed to liquid loading they are anticipated to face during their service life, simulating hydrostatic pressure is an incredibly critical part of the safety precautions. For instance, if oil storage tanks cannot sustain their liquid load in addition to any other extra pressure, the shell of the tank or container would burst.
One would need to confirm the hydrostatic pressure using techniques from finite element analysis (FEA) to calculate the amount of stress and displacement imposed on a structure due to liquid loading.
Find the Right Finite Element Analysis consultants Simulation Service for You
Mechartés is a premier engineering simulation service provider. We are experts Finite Element Analysis consultants and computational fluid dynamics (CFD) simulations for the automotive industry.
We provide best-in-class simulation services to clients from all around the world. Moreover, we offer customized solutions tailored to suit your needs and specifications.
At Mechartés, you can access world-class consulting services to provide customized solutions for your project. We guide enterprises and organizations on FEA simulation challenges through a broad range of consultancy services.
We are committed to exceeding expectations and delivering jaw-dropping successes that will take your project over the top! Reach out to us today!