We live in a digital age where technological innovations boom every day. Innovations in computers, smartphones, and other electronics are no exception. With every new trend, there is an increased need for technology to recognize and optimize the safety and efficiency of the innovation, especially when it comes to the cooling systems in electronics.
In electronics, cooling or thermal management of the components has been seen as a high necessity. In addition, new trends in electronics and miniaturization with increased power density due to densely populated packaging and high processing speeds have called for better and more efficient cooling systems in electronics, specifically in CPUs.
Thermal management in electronics focuses on uniform heat dissipation with adequate heat flux removal. Thermal management is also essential for devices to make them perform at optimal capacity and within design parameters.
What Happens When CPUs do not have Adequate Cooling Systems?
Efficient cooling systems in a CPU can:
-
Increase the lifespan of the component
-
Make the CPU units perform at optimal levels
-
Help microprocessors save energy
-
Prevent system malfunction or catastrophic failure
-
Improve heat removal rate and maintain optimal operating temperatures for the CPU with the help of coolants for heat transfer
Hence, robust cooling systems are being implemented in CPUs by leading manufacturers and PC hobbyists to protect the integrity of the chip and enhance its performance.
How do Cooling Systems in CPUs work?
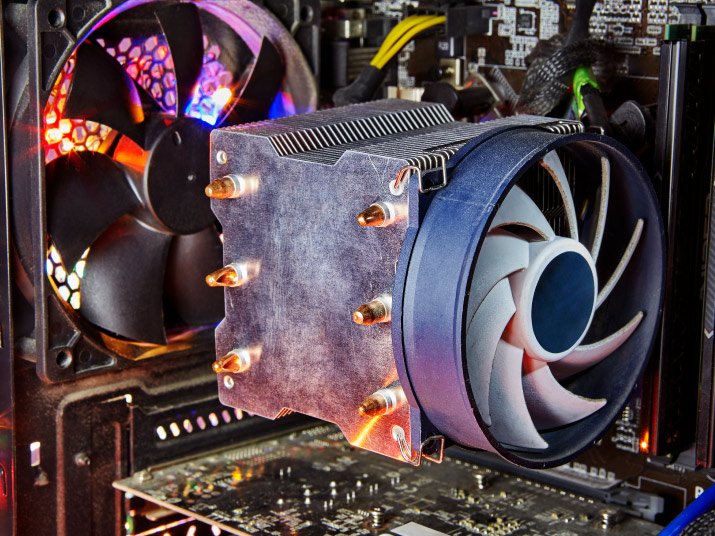
Generally, in electronics, four main thermal cooling techniques are widely used:
1. Natural Convection Cooling
Natural convection cooling systems employ a passive heat sink made with copper or aluminum sheet. The rising heat drives the air, which pulls the cold air below.
2. Forced Convection Cooling
Forced convection cooling uses artificially produced air velocity from a fan in the system to aid cooling levels.
3. Fluid Phase Change Cooling
Fluid phase change cooling is also referred to as re-circulation cooling. A closed-loop heat pipe is integrated into the system to allow accelerated movement of heat transfer with the concept of evaporation and condensation in the structure.
4. Liquid-cooled Cooling
Liquid-cooled cooling systems use cold plates, a heat exchanger, and a pump circulating cold fluid past a heat source.
CPU Cooling Systems
CPU cooling systems employ the forced convection cooling technique. In a CPU, the cooling system moves the heat away from the sensitive and comparatively expensive parts of the unit with the help of heat pipes and heat sinks.
The heat pipes act as a device for rapid heat transfer with high thermal conductivity. The heat pipes are 100 times more effective than normal metal at conducting heat.
The heat pipes in the CPU push the generated heat into the heat sink. The heat sink increases the contact area of the heated air to accelerate heat dissipation with natural or forced convection to the surrounding environment.
Optimizing Cooling Systems in CPU with CFD Simulation
In order to make the cooling systems more effective and efficient, experts recommend using CFD simulation in CPU models.
Cooling techniques in electronics is a tedious process and is challenging to arrive at the right technique and parameters, usually derived by trial and error or standard prototype testing. But, this approach is expensive and also time-consuming.
CFD simulation for heat transfer in CPUs helps visually observe and study heat and fluid flow inside the unit through the various components of the CPU.
In addition, CFD simulations allow for fast designing and engineering CPUs by evaluating and optimizing heat management using robust geometry prototypes and working conditions.
For CPU, CFD simulation allows engineers to test different strategies and experiment with the heat management process by adjusting the size and number of heat pipes, increasing the number of heat sink fins, adjusting the thickness, use of surface treatment, radiative paint, and other parameters to produce optimal heat loss with thermal radiation or by using other materials to induce the same or better effects.
When testing a model with CFD Simulation, experts often use a target temperature and run models against them to produce expected results. When one model does not work out, engineers have the option to work out other models until the desired results are achieved.
This is not feasible with physical prototypes. Instead, CFD Experts use many testing scenarios with simpler workflows and accurate turnaround times to arrive at the optimized design.
Once the design has been tested and optimized for complete cooling efficiency and performance, it is taken to the next stage of the designing process: physical prototyping. But, only one prototype is needed before taking the design to the market.
Many CFD Experts used cloud-based simulation to make computing processes faster and easier. Cloud-based CFD simulation allows CFD Experts to perform accurate, heavy, high-fidelity simulations with increased accessibility irrespective of the engineer’s hardware capacities. In addition, cloud-based CFD simulations can run models parallelly, decreasing the run time from weeks to hours.
Summarizing
CFD Simulations make designing and engineering CPUs hassle-free, fast, and cost-efficient. CFD simulations speed up the design and optimization process by removing the need for multiple prototypes. In addition, various CFD techniques can increase the efficiency of cooling systems in CPUs.
CFD Experts at Mechartes are experienced in conducting CFD simulations for CPUs, electronics, and more practical applications with the help of robust technology and trends in CFD. Our proven methods enable manufacturers to estimate the right cooling technique and system for CPUs and other electronics.
Reach out to us to know more about our CFD Simulation and validation services.