Vibration in pipelines causes many significant problems to the piping systems, such as fatigue failures, rapture leaks, etc. Flow-induced Vibration (FIV) study is an effective way to tackle these vibration-induced problems.
FIV study can help analyze fluid flows and vibration phenomena and predict vibration-induced concerns in pipelines to optimize them and ensure the piping system can remain operational for an extended period.
In this article, we will learn why an FIV study is crucial for piping systems and how to conduct it for piping systems. Let’s first understand the issue of vibrations in piping systems and the extent of damage they can inflict.
Flow-induced Vibrations and Their Effects on Piping Systems
As the name suggests, flow-induced vibrations are mainly caused by uneven flow inside piping systems. When fluids flow through pipes, some undesirable phenomena such as pressure fluctuation, vortex, and turbulence can occur, and as a result, vibrations are created inside pipelines.
The vibration originating from a vortex of fluid is called vortex-induced vibration, which happens when fluid passes through a bluff or cylindrical portion of pipes such as elbows and tees and creates vortices. These vortices exert force constantly on pipes leading to vibration.
The vibration caused by turbulence is known as turbulence-induced vibration. Turbulence usually occurs when there is an obstruction, sudden change of flow path, or sudden acceleration of the velocity of the fluid.
Consequently, these vibrations lead to periodic forceful exertion on the body of pipes which causes fatigue failures, rapture leaks, and other damage to the piping system. This makes it imperative to carry out an FIV study for piping systems to evaluate and analyze them and develop mitigation measures.
FIV Study for Piping Systems: An Overview
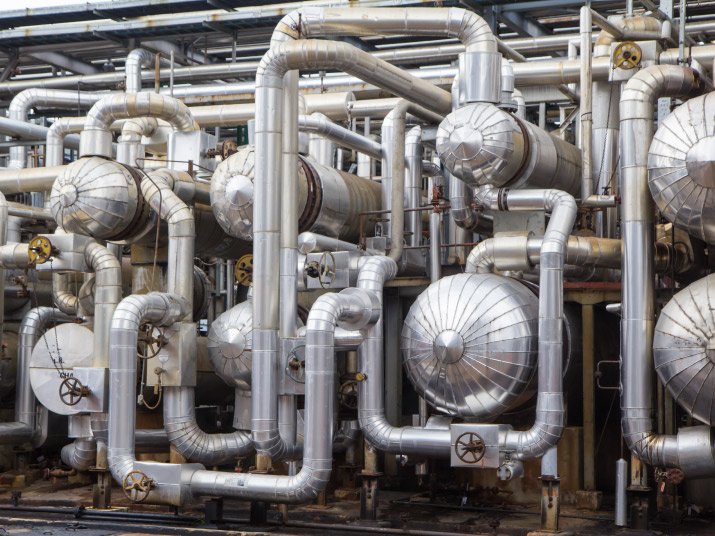
FIV study involves assessing vibration frequencies under different flow conditions and then helping to provide mitigation measures to prevent vibrations.
FIV can be studied using both experimental and numerical methods.
-
An experimental study
It uses a scaled-down or full model to analyze vibration frequency under different flow conditions and predict vibration-induced damages to the piping system.
-
A numerical study
This is carried out using CFD tools to simulate fluid flow under different conditions. The numerical method is fast and accurate and can be used for more complex piping systems than the experimental method.
Different design configurations and flow conditions can be studied in the numerical method. It can also identify different vibration-induced damages to prevent them.
The CFD simulation for the FIV study involves several steps to simulate fluid flow and predict vibration occurrence in piping systems.
What Are the Steps Involved in the CFD Simulation for the FIV Study?
The typical steps in the CFD simulation are as follows:
1. Define Geometry
The first step of the FIV study using the CFD tool is to develop a 3D model of piping systems with geometry and dimension in a CFD computer program.
The geometry is paramount for the numerical and helps predict the correct flow behavior. It must be accurate for the actual system, including all components such as pipes, fittings, valves, pumps, etc., to get a better result.
The geometry should be well-defined and clean to achieve an accurate simulation and meshing. It should also be compatible with a simulation software as there are different prerequisites for different simulation programs.
2. Define the Boundary Conditions
In the second step, the boundary conditions, such as inlet and out boundary conditions, wall boundary conditions, symmetry boundary conditions, etc., are required to be specified and rendered in numerical in the simulation.
Inlet boundary conditions are the values of fluid properties such as velocity, pressure and temperature, and other related fluid flow parameters at the inlet section of the simulation of piping systems. Also, the inlet value should be consistent with the actual system which is being modeled.
Outlet boundary conditions are the specific values of fluid properties at the outlet section of the piping system simulation. Wall boundary conditions are the particular value of fluid properties at any solid surface or wall inside the simulation.
3. Mesh Generation
In this step, CFD experts disintegrate geometries into a large amount of small mesh to represent the fluid flow and study fluid behavior at every mesh. Mesh generation is a critical part of the FIV study that defines the accuracy of the simulation.
The mesh should be created in such a way that it captures the fluid flow accurately to predict the vibration frequencies. Additionally, the mesh should meet the basic criteria such as aspect ratio, skewness, orthogonality, etc.
4. Solve the Equation
Subsequently, the complex equations of fluid mechanics are solved by CFD experts to simulate fluid flow and to calculate fluid properties such as velocity, pressure, and other physical properties of the fluid.
5. Post-processing
When the simulation is done, the tool analyzes the result and predicts the behavior vibration inside piping systems. This process involves calculating the natural frequency of vibration, evaluating the vibrational amplitude, and predicting the potential area of concern.
The accuracy and reliability of CFD simulation for FIV study depend on mesh quality, turbulence model, and the numerical method employed. Therefore, careful verification and inception of data such as geometry and dimensions are essential to ensure reliable simulation results.
Conclusion
Evidently, the FIV study is an effective way to analyze and predict vibration-induced problems in pipelines. They can also help to design mitigation measures to tackle vibration issues and deliver reliable operations of piping systems.
Therefore, FIV should be conducted regularly to maintain piping systems’ efficiency and safe operation.
However, it is to note that FIV study using numerical methods requires expertise and experience in CFD and fluid mechanics to get accurate and reliable results and predictions.
We at Mechartes provide exceptional CFD simulation services for piping systems, including FIV studies for piping systems.
With our experienced team of CFD experts and skilled engineers, we have provided 100% reliable results to numerous clients and improved their systems.
We are also a leading expert in FEA and CFD simulation for other industries, such as oil, gas, water treatments, and other plants.
Talk to us to learn more!