The finite element method is a technique used to analyze and understand physical phenomena and their effects on an object. It is predominantly used to study physical phenomena like wave propagation, structural or fluid behavior, and thermal transport with the help of mathematics.
When solving FEM problems in a computer, all issues are entered in Partial Differential Equations (PDEs). PDEs are generally hyperbolic, parabolic, or elliptic. Then, the conditions of the boundaries or initial conditions are fed into the software, and the inputs are evaluated and resolved.
Depending on the type of PDE, the values are chosen and solved using specific laws:
-
Elliptic PDE uses Poisson Equation
-
Hyperbolic equations are solved using Wave Equation
-
Parabolic equations are solved using Fourier Law.
The Finite element method (FEM) and finite element analysis (FEA) are widely used by engineers to identify the weak spots and make improvisations.
Difference Between FEM and FEA
FEM provides a numerical solution for complex problems by breaking them down into smaller parts. Usually, mathematical problems that are too complex are solved using FEM.
Engineers developed this in the mid-1950s to establish a practical design that is not perfect for application. Engineers can use the inputs from FEM to improvise and enhance the design to suit the application. In addition, FEM helps solve complex numerical problems with some level of errors and gives solutions that can help rectify those errors.
In FEA, the mathematical solutions solved using FEM are used in a simulation. These simulations can assess and give insights into how a design and its structural integrity will perform under real-world stresses.
The entire model is broken down into elements in a mesh, and these individual elements are tested under simulated stresses to understand their stability and integrity.
In simple words, FEM is used to solve complex mathematical problems which can be used in FEA to study the structural integrity and performance of a design under the influence of physical phenomena.
Different types of FEM
Engineers have made several advancements in FEM techniques to counter shortcomings and enhance simulations and procure accurate results.
Extended Finite Element Method (XFEM)
XFEM method was introduced to overcome shortcomings faced with continuity of displacement in the Bubnov-Galerkin method. XFEM works through shape expansions with Heaviside step functions. Nodes can be assigned additional freedom around discontinuity points so that jumps can be considered.
Generalized Finite Element Method (GFEM)
It is a combination of traditional FEM and meshless methods. Engineers introduced GFEM to combat re-meshing around singularities. The global coordinates determine shape functions multiplied by partition by unity for local elemental shape functions.
Mixed Finite Element Method
Incomrpessibility and constraints are imposed using Lagrange multipliers which are solved independently due to added levels of freedom. The equation system is solved like a coupled system of equations.
hp-Finite Element Method
hp-FEM combines automatic mesh refinement (h-refinement) and increases the order of polynomials (p-refinement). With this method, elements can be divided into more minor elements, and each element can have different polynomial orders.
Discontinuous Galerkin Finite Element Method (DG-FEM)
Engineers can use this method to solve hyperbolic equations using finite elements. Bending and incompressible problems can also be solved using this method. Additional constraints to the weak form and a penalty parameter and other equilibrium stresses between the elements can be added using this method.
Applications of FEA and FEM
Engineers introduced FEM to study designs for aerospace and civil engineering.
FEM is currently being used in several industries that need to study physical phenomena and their effects on a design in fields like biomechanics, thermomechanical, fluid-structure interaction, biomedical engineering, ferroelectric, thermo-chemo-mechanical problems, piezoelectric, and electromagnetics.
FEM principles can also be applied to CFD to study the thermal dynamics of a structure. For instance, in a particular simulation, you can find out the temperature in an object at a specific time and study its rising/decreasing patterns over time.
6 Advantages of Using FEM and FEA
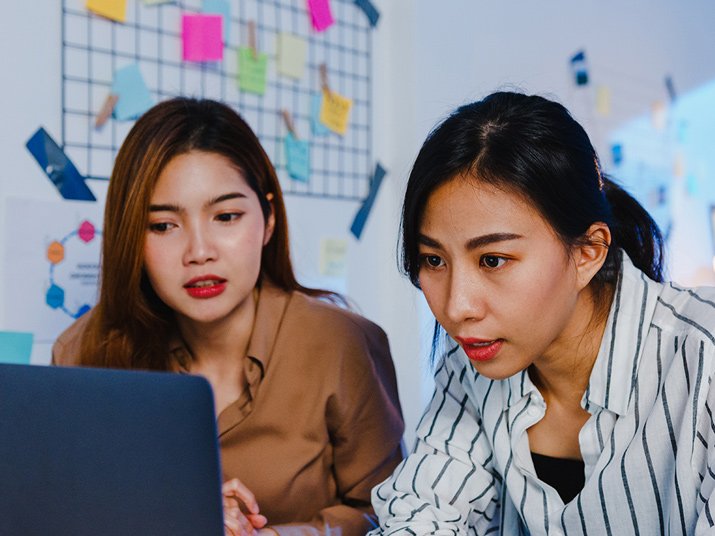
FEM is a widely used analysis technique in the engineering community. It gives compact and straightforward results that are useful in the design and construction stages of projects. It is incredibly beneficial to study any object that physical phenomena can influence.
1. Modeling
Engineers and designers can create a model of an object even if they are geometrically complex or irregularly shaped. Interior and exterior features of the model can be designed for analysis which can significantly impact the performance of an object. FEA can be used to understand small components and elements of the design that can affect the structural integrity of the whole object and identify vulnerable points of a design.
2. Adaptability
FEA and FEM eliminate the need for multiple physical prototypes to test efficiency and integrity in the design stage. Modeling the design on computer software vs. creating a physical prototype takes a few hours and saves a lot of costs, time, and resources.
3. Accuracy
Manually created prototypes can have deformations or fail to replicate complex designs. FEA can deliver accurate design by feeding the correct numerical values and enough data to run the simulation. FEA dramatically minimizes the risk of computational and artificial errors.
4. Time Dependant Simulations
Time dependant simulations, whether longer or shorter time steps, can be analyzed using FEA. Phenomena like crash analysis that require shorter time steps and tear and wear stresses over larger time steps can be analyzed using the various techniques of FEA.
5. Boundaries
Boundary conditions can be defined on FEA to understand how the object responds in a specific condition. These boundaries can include point forces, distributed forces, positional restraints, and thermal effects.
6. Visualization
FEM solutions can be visualized with detail on deformations and vulnerable spots on the design. This helps engineers and designers easily understand the problem and create an alternate design to withstand the conditions. Engineers can build quality designs using visualized data from FEM and FEA.
We hope this article helped you understand the difference between FEM and FEA and how they can be used together to yield quality and intact designs with the minor investment in prototypes at a reduced time frame.
With the help of Simulation experts and validation services from Mechartes, FEM & FEA can be applied to your designs, identify weak spots or vulnerabilities, and make improvisations for better performance and structural integrity of the design.