Computational fluid dynamics, or CFD, is a branch of fluid mechanics that uses numerical analysis and data structure methods to identify answers to fluid flow-related issues. Many experts in this field provide CFD analysis services to assist engineers in swiftly and accurately resolving their fluid flow issues.
CFD uses Navier-Stokes equations to forecast the flow of any liquid or gas. These equations aid experts in precisely calculating the temperature, density, velocity, and pressure of any flowing fluid. CFD for HVAC systems uses the same principle to solve various problems related to thermal comfort and temperature regulation in engineering projects.
This article will show how CFD for HVAC systems is an efficient solution and its various use cases.
CFD for HVAC Systems: A Brief Introduction
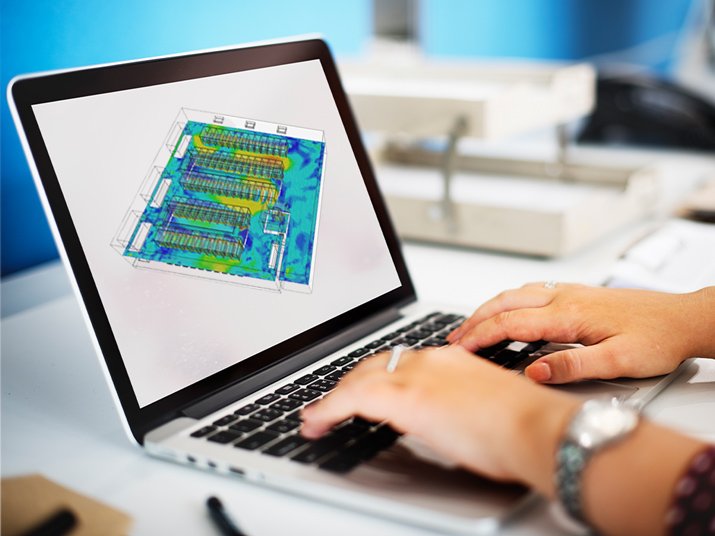
Buildings must offer a comfortable climate that protects people from the heat and cold outside homes, schools, or workplaces. Lack of thermal comfort in an enclosed area can harm overall health and even impair concentration, and it is crucial to guarantee the best possible internal thermal comfort.
CFD for HVAC systems can be used for the design evaluation and analysis of the HVAC systems. Thermal comfort can be measured, analyzed, and optimized when fluid flow simulation is used in HVAC design.
CFD for HVAC Systems aids in the investigation of airflow patterns, temperature distribution, radiation, and heat transfer. The software can display the locations of heat loss, inadequate ventilation, and cold spots. Various stakeholders can add data throughout the CFD simulation, and designers can inspect and test every HVAC system component.
Engineers may analyze new and existing structures before suggesting improvements, lowering costs and necessitating fewer physical resources because they have access to precise data and simulation findings.
Role of Thermal Comfort in Buildings
Regulation in public areas defines thermal comfort and indoor air quality. Building regulations establish criteria for droughts, heating, cooling, pollutant management, and smoke extraction. Radiative warmth can be influenced by constant and variable variables, such as the number of people entering or leaving a room. An engineer may view and evaluate the pertinent aspects using CFD modeling, ensuring that the design of indoor spaces will be pleasant in the face of unexpected droughts or temperature changes.
CFD can aid in optimizing HVAC system performance. Evaluating natural convection, drought velocity, and temperature dispersion are possible—these and other simulation findings aid in creating a comfortable and effective design that adheres to regional requirements.
CFD for HVAC systems may be performed to test and enhance designs and model different heating or cooling sources. Engineers can choose the optimal locations for heating, cooling, or ventilation systems and develop thermally optimized HVAC systems.
Use Cases of CFD For HVAC Systems
Air conditioning systems, fans, and blowers are frequently installed in residential and commercial structures to maximise thermal comfort. Here are some examples of how CFD for HVAC systems can regulate thermal comfort.
Automotive Cooling Systems
Powerful 15L diesel engines produce an unfavorable high-heat ejection rate. To meet airflow and top tank temperature requirements, vehicle front-end cooling packages must be correctly sized, built, and installed in high horsepower engines.
Generally speaking, the airflow is restricted more when the radiator is larger. Early in the radiator design phase, assessing pressure drop throughout the radiator component is helpful based on the specified fin density. CFD for HVAC system techniques can be used to arrive at an optimum cooling package before it is connected to the vehicle’s system.
A cooling fan, essential for delivering ambient airflow when the car is parked or idle, is typically included in cooling packages. CFD analysis can be conducted under different fan speed scenarios. Conjugate heat transfer may be necessary for some circumstances to anticipate the top tank temperature correctly.
In other instances, a system limitation curve can be identified using a cold flow CFD technique to simulate various driving situations for cooling package design optimization: cold flow, warm flow, and hot flow conditions.
Blade-less Fan
The “Dyson Air Multiplier,” a blade-less fan created by Dyson, is frequently regarded as a creative and affordable cooling solution for home appliances. A potent approach for assessing how well such a novel design performs in terms of airflow is CFD.
The RANS method (Reynolds-averaged Navier-Stokes) predicts local airflow acceleration over a ramp concealed inside the plastic fan cover. Along with the mixing turbulence, the device’s hidden airflow acceleration boosts air momentum.
When there is a high-speed flow in the internal ducting tube, air mass flow is enhanced even more. As a result, the unfavorable, irregular flow distribution previously observed with traditional blades is no longer present in this circumstance. The blade-less configuration makes it simple to produce regular airflow distributions, which improves thermal comfort.
Blowers
HVAC blower noise has been extensively acknowledged as an engineering concern for the past few years. A blower and a single ducting unit are typically used in HVAC system designs in the automobile and aerospace industries to help supply air cooling flow to passengers. The system does this using various registers and vents close to the passengers.
The blower must be correctly engineered to supply the necessary mass flow rate and satisfy the cabin’s thermal comfort needs, which exposes it to solar radiation in the worst-case scenario. For these comfort needs, high-speed blowers are ideal.
However, the turbulence-related noise produced by such fast-moving blowers is unpleasant, and it has been discovered that such noise propagation frequencies are upsetting to passengers.
Additionally, it has been discovered that turbulence noise is amplified inside non-uniform cross-sectional ducting systems, where most of the airflow undergoes repeated separation and reattachment cycles depending on the ducting shape.
The maximum allowed distance and the ease of installation play a big part in determining the ducting form. Quantifying the noise level of high-speed moving blowers for target settings is exceedingly challenging due to the complicated flow structures produced inside the HVAC ducting system.
CFD for HVAC systems, the noise source may be assessed early on in the blower design phase. It is possible to identify a nonlinear noise source from an advanced turbulence model. A linear noise propagation code can be used to analyze sound propagation based on an analogy formulation for acoustics.
Solving Complex Engineering Challenges with Mechartes
With a professional approach and an engineering attitude, Mechartés focuses on delivering accurate simulation results. We produce accurate and reliable outcomes with cutting-edge methodologies, simulation algorithms, computer capacity, and more than 16 years of industry experience.
Reach out to us to know more about our comprehensive solutions for CFD for HVAC systems.