CFD analysis and simulations have gained more and more attention in recent years due to their ability to provide engineering information about products, such as their efficiency and resistance, efficiently and cost-effectively.
With such analysis, engineers and designers can simulate a virtual test lab without having to prototype, and they can do so while still in a CAD design phase.
While this is a significant advantage, it does have a downside: Are the results accurate? Are the common errors a part of this package? Is there a chance to avoid such mistakes?
We will investigate five common mistakes that one should avoid when doing a CFD analysis. Let’s get started!
Five Common Mistakes in CFD Analysis & How to Overcome Them?
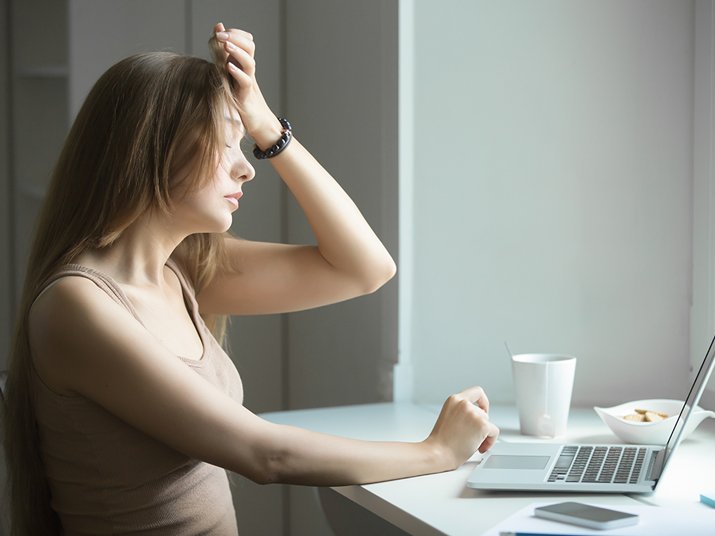
There are multiple sources of errors in CFD Analysis. It could be your physical models, turbulent models that don’t work, inefficient combustion models. You may also have numerical problems resulting from incorrect modeling of equations.
There are many reasons for this, including improper convergence, dissipative schemes, grids that don’t resolve physics, schemes that cause oscillations, etc.
The solution you come up with cannot be proven mathematically to be a valid one. A CFD solution can’t be subjected to strict error estimation.
Verify that you don’t fall into the bucket of common mistakes. And how do you do that? Scroll down!
1. Quality of mesh
CFD software uses meshes as a geometrical structure to perform calculations. The meshing process is a crucial part of any analysis, even if it’s time-consuming. For good results in a later phase, mesh quality must be verified after creation.
How can this be accomplished?
Imagine the solution you are trying to achieve and refine your mesh near the areas where gradients are expected to be high (i.e., temperature and stress variations).
However, what if you cannot imagine the solution?
Well, try meshing for the first time and check the results when you run CFD analysis. Then, based on these results, make a second mesh.
Additional tips
-
Densify meshes where gradients are high
-
Resolution of wall-bounded shear layer by y+ <1
-
As much as possible, keep the wall orthogonal
-
Simulating meshes with less orthogonal quality requires a lower relaxation factor
-
The walls would be rendered incorrectly gradient if the mesh were highly skewed. The results could be unbounded or divergent.
-
When the cells are highly skewed, the flux gradients near the walls could be incorrect.
2. Never complicate your CFD analysis
Keep your analysis simple. Sounds easy? But, this is probably the most challenging task. Several switches are available for any user to toggle on and off in CFD software. Each switch impacts the simulation differently.
For example, you can activate or disable turbulence, rotation, combustion, heat exchange, phase change, radiation, chemical reaction, gas compression, gravity, etc. However, in most simulations, only a few switches have significant effects.
Thus, the rest of them have negligible effects, so they can be turned off without impacting the simulation. As a result, we can use less time and produce more accurate results by avoiding redundant analysis.
Additional tips
User experience is paramount, but at the same time, the logic applies as well. For example, in a simulation of an impeller, heat exchange and gravity are less critical, whereas rotation and turbulence are crucial.
When it comes to forcing, convection gravity plays only a minor role. Gas compressibility cannot be ignored inside turbomachinery.
3. Did you check your convergence?
The most basic rule of CFD analysis: make sure the simulation convergence reaches the appropriate residual level.
How do residuals work? They are a set of parameters. Using such indicators, users can determine if the existing solution represents the exact physical solution defined with the given mesh and boundary conditions. In addition, it indicates how far from the final iteration we are or if we should proceed a little further.
CFD solutions are based on steady simulations, and even when the simulation is steady, the residual (error evaluation) gets smaller with each iteration. Unfortunately, this process usually takes at least a hundred iterations (thousands for big geometries).
Simulating for a low number of iterations won’t give you accurate results. Is there a practical tip? Before you stop the simulation, make sure residuals are below 10^-4.
4. Are you choosing the suitable CFD model?
Usually, when it comes to solving models, things are very complex. For example, CFD users can choose from various compressible flows, turbulence, heat exchange, mixtures, etc.
Firstly, we need to determine the primary purpose of our simulation: should we measure heat flow? What about friction coefficients? Answering these questions allows us to obtain all the information we need for our CFD simulation.
Mechartes CFD solution offers easy-to-follow instructions to help users get started. So get in touch to begin your simulations right now!
Additional tips
Select the correct turbulence, multi-phase, and combustion models to achieve desired results.
5. Boundary & input data
The inlet conditions need to be rechecked for
-
A uniform or non-uniform velocity profile should be present at the inlet.
-
When a long duct is incorporated into the inlet, use a fully developed velocity profile.
-
If the velocities are significant and the inlet sections are located outside the main domain, use the mass flow rate.
Please check for the following outlet boundary condition:
-
If the pressure field is known, use a fixed boundary.
-
If gradients at the outlet section are negligible, use the outflow boundary.
Finally, the results aren’t helpful if they aren’t analyzed. CFD simulations generate a lot of data. We need to process these data to extract the critical information required to understand the simulated phenomena’ details.
No matter what, we are looking at forces, heat exchange, friction, gas concentration, temperature, and fluid-wall interaction. There are so many variables that it is impossible to group them into one category.
With Mechartes you have complete control over these results with our team of CFD analysis and simulation experts. Need help on advanced methods, simulation algorithms, and computing power? Get in touch!