1. Objective
The main objective of the work for the Tower Columns is to study the following parameters.
-
Study of the Flow Patterns inside the column.
-
Maldistribution inside the vessels
-
To verify the droplet size and ensure the dry gas outlet as per process requirements.
-
To track the droplet flow
-
The studies were carried out to study the velocity distribution of the fluids.
-
To check the design will meet the performance specifications proposed by the client for the maximum flow rates proposed.
2. Description
The process gas quench tower is a pressure vessel where process gas from Process Gas Separator enters at high pressure and temperature. The process gas quench tower reduces the temperature of the process gas from 119.8°C to 47°C. The pressure of process gas entering the quench tower is 5.4 bar (g).
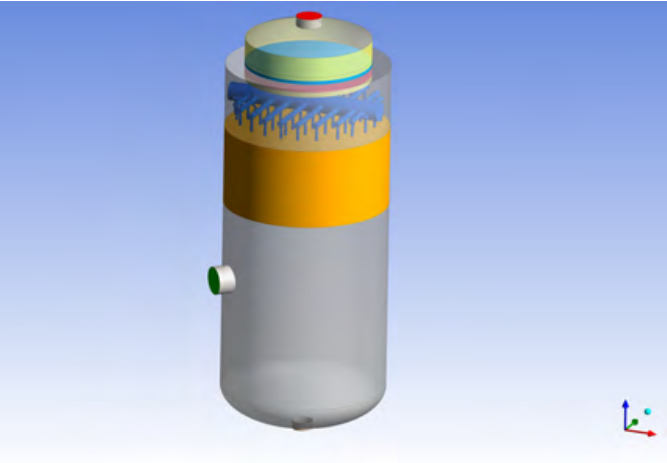
The temperature reduction in gases is done by injecting cool water (38°C) from distributor, evenly across the cross-section of the quench tower on a 3m thick packed bed. The liquid content from the process gas is separated by VV type demister and a 152 mm thick demister pad.
The end to end length of the quench tower is 15,897 mm with an internal diameter of 5,785 mm. CFD simulations were carried out to study the flow behavior inside the vessels with changing the demister pads in the vessel.
3. Modeling Approach
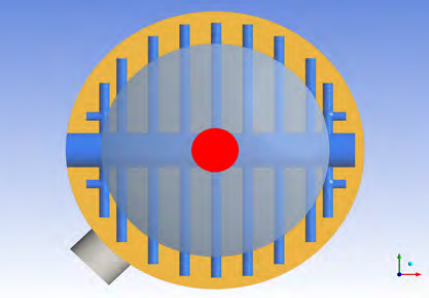
The heat transfer in CFD packed bed equaling the heat of condensation was predicted based on design process data sheet and modeled as heat sink in the packed bed. The water will enter as fine droplets at inlet, this has been modeled based on Discrete Phase using DPM modeling approach.
As the droplet diameter is unknown several droplet distributions are iterated in this study. RANS based Realizable k-ε turbulence model is used to model flow turbulence.
The inlet gas flow rate is 493,408 Nm3/ h at the pressure of 5.4 bar (g) and temperature of 119.8oC. The total mass flow rate of cooling water is 3,538.702 Tonnes per hour. The total water droplets entering the quench tower in Discrete Phase is 111,582.02 kg/h.
4. Conclusion
CFD simulations were carried out to study the flow behavior inside the Process gas quench tower with different demister pads inside the vessel. It was observed that the increase in demister pads increases the pressure drop in the vessels, however no significant variation in flow characteristics is observed.
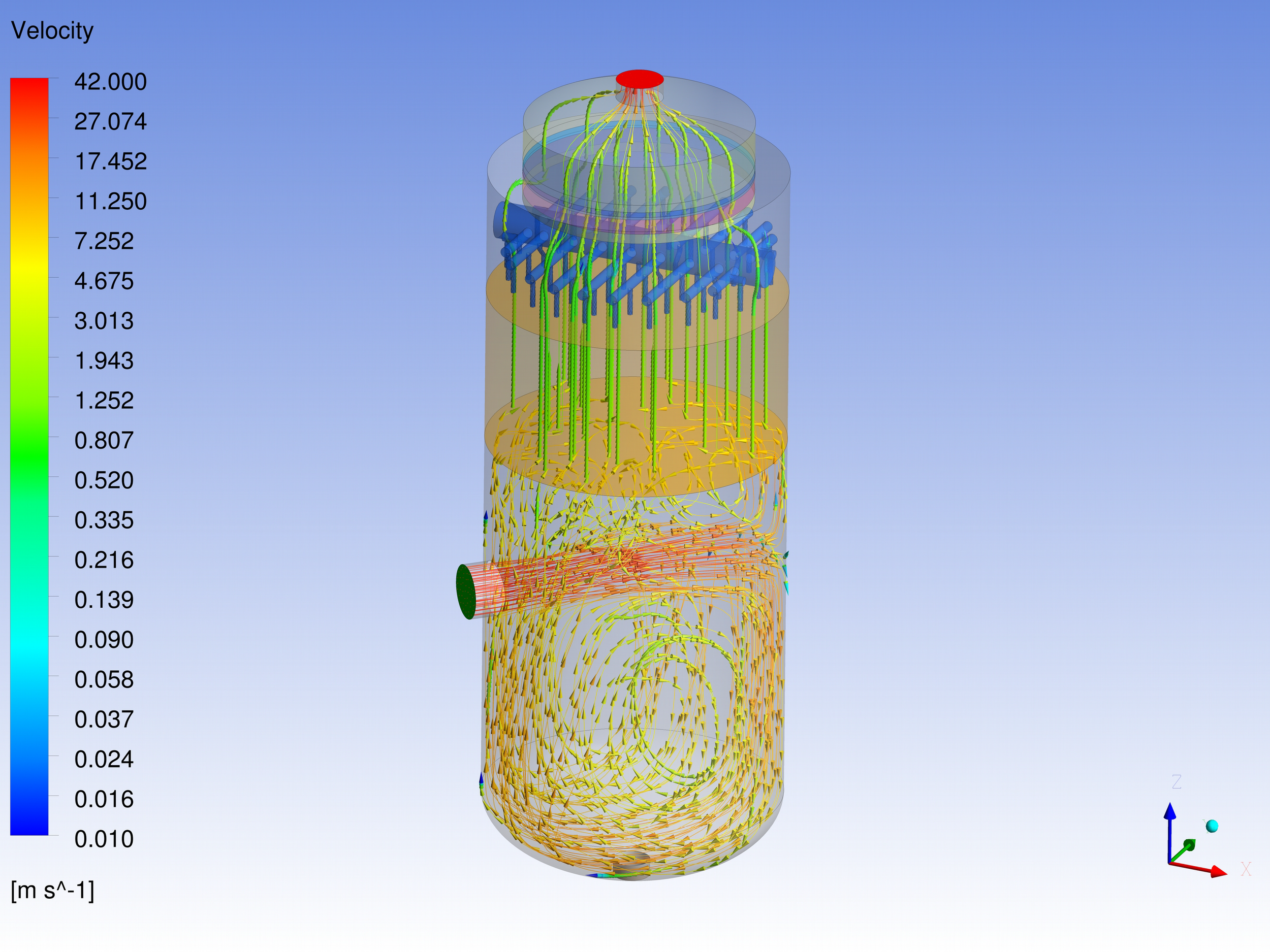
With new demister pads, the increase in pressure drop across process gas quench tower is calculated as 248 Pascals. The velocity profile at the cross-section in process gas quench tower were observed to be even throughout the crosssection.
Due to the even distribution, the water droplet loading across the demister is also equally distributed across crosssection. No major impact on liquid carryover reduction is observed by adding the additional demister.