Have you ever wondered why seemingly well-designed components can fail after a period of use? The truth is, there’s rarely a single reason for design failure. It’s often a combination of hidden stresses lurking beneath the surface. This is where Fatigue Analysis Services come in.
Some factors leading to a decrease in performance or failure of a design, which Fatigue Analysis Services can help identify and mitigate are:
-
Stress or material failure is where the material used for the component fails over time due to stress or lack of durability.
-
Stability failure is widespread among thin or slender structures.
-
Failure due to deformation is when a component or a system fails due to excessive deformations. A slightly bent fan blade that gives in or fails to regulate the heat in a room, even if the deformation is minor.
-
Vibrations can be associated with fatigue in a cyclic load where the component fails when resonance is in the background. The vibrations may not be a disturbance at first but ultimately may cause the component to fail.
-
Finally, fatigue is a significant reason why designs or components fail. This is very common among a design operating with a cyclic load, whether static or changing loads.
The design may seem fine in the beginning. However, after a few years, it will eventually fail.
Fatigue by Definition: The Five Box Trick for Fatigue Analysis Services
Fatigue can be defined as a design’s failure due to repeated or varying loads, which never reach a level significant enough to cause a failure in a single application.
Fatigue is sometimes considered the initiation and growth of a crack due to a pre-existing deformity that ultimately reaches a threshold point where the component separates into two or more pieces.
What is the purpose of fatigue testing?
It is to understand the tolerance of cyclic loading and the structural durability of material under stress.
Fatigue analysis services is usually done in two methods:
The Stress-Life (S-N) method, also known as the Total Life method, does not distinguish between the initiation or growth of a crack. The Local Strain or Strain-Life (e-N) method, or the Crack Initiation method, concerns fatigue analysis services when a crack is formed.
The Five Box Method for Fatigue Analysis Services
Every time Fatigue analysis is conducted–be it with FEA Methods or other techniques–the five-box method can help evaluate values and interpret results accurately.
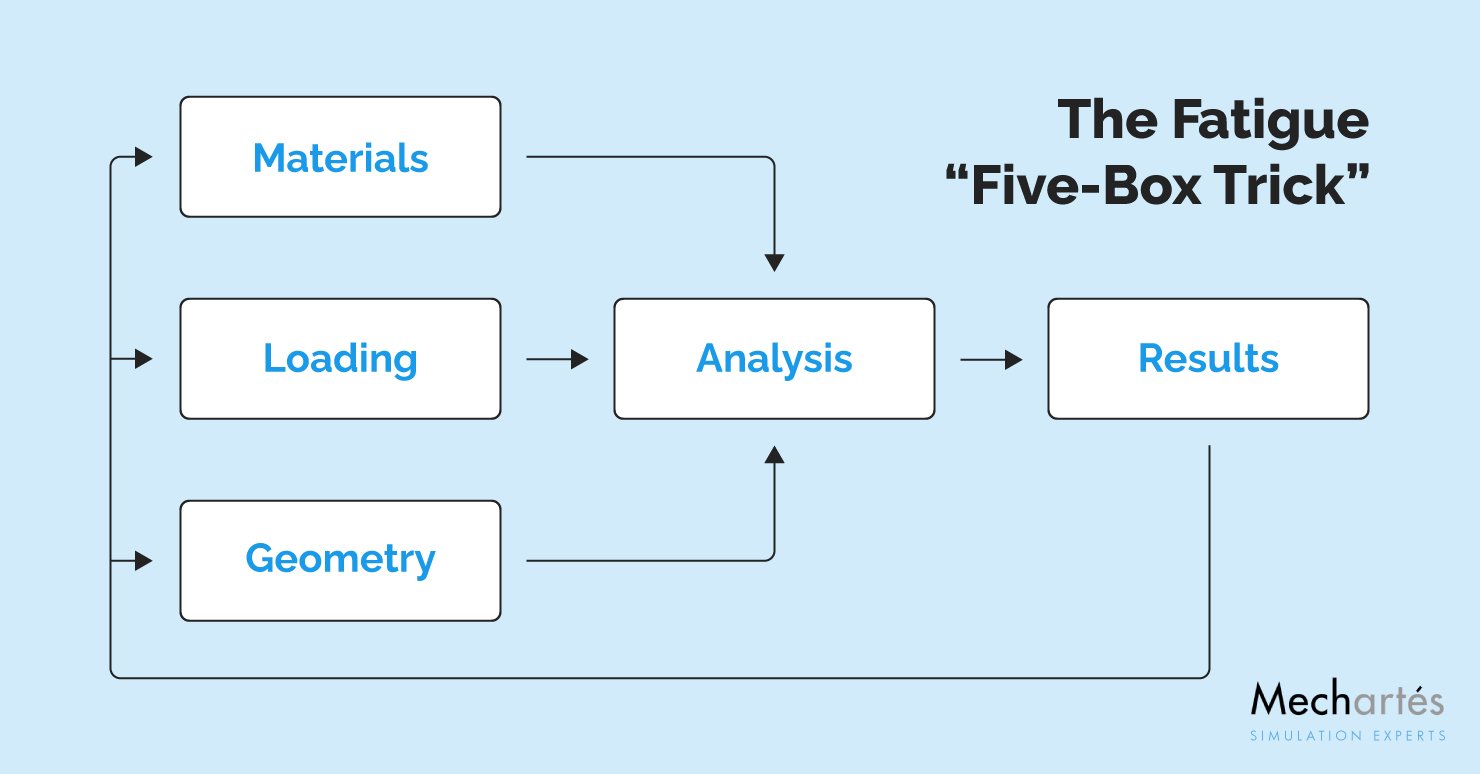
The first three boxes are the inputs. Box four depicts the analysis, and box five concerns the results and interpretation of the analysis.
1. Cyclic Material Data: When materials are exposed to cyclic loads, they behave differently than a static or monotonic load. The load steadily increases with a monotonic load until the test component breaks. Then, the loading is reversed and cycled with a cyclic load until failure occurs at different levels. Sometimes, these parameters vary based on the technique used for fatigue analysis services.
2. Service Loading Data: Accurate loading specifications must be loaded for fatigue life prediction. Depending on the type of analysis, the loading can be made in different patterns, such as time-based, frequency-based, or spectrum-based. For example, when using FEA Fatigue analysis services models, the loading parameters are usually force, pressure, temperature, displacement, etc.
3. Geometry Data: The geometry input refers to the stress concentration factor Kt, which is defined to relate the measured response at the failure location. The Kt is applied over the finite element model with added local stress concentration factors to estimate geometry toughness and longevity.
4. Analysis: The data loaded into the system determines the accuracy of the analysis. Any minor error will be magnified during the analysis as it is a logarithmic procedure. For example, a 10% error in loading could result in a 100% error in the predicted fatigue life. Hence, the values mentioned above must be accurate. The analysis indicates the stress and fatigue life calculation in an FEA Analysis.
5. Results: Post-processing results can be in the form of a color or tabular listing of values that specify what effect each input value has on the component’s fatigue life. The input values can be changed to see how they affect the life prediction.
This is usually referred to as a sensitivity or “What If” study. It can be used to understand the component’s threshold. For example, this study can estimate the highest value of each input that does not break the component but is also not too low. That helps with design optimizations using fatigue life predictions.
FEA Fatigue Analysis Services
Using fatigue FEA Analysis allows you to estimate the permissible value for the component’s capacity. Sometimes, FEA Analysis can also compare values and interpret the allowable value.
FEA Analysis can verify whether the component can function with the given inputs or not. It can also be used for optimizations, estimating the margin of safety and the number of cycles of loads the component can endure.
In machine design practices, 99% of the FEA are linear analyses involving small material deformations. For irregular geometries, small meshes and notches are used to detect stress.
The conventional procedure for carrying out FEA Fatigue Analysis is first to calculate the maximum and minimum stresses under fatigue loads. Irregular geometrical stresses are not taken into account for nominal stress calculations.
Secondly, the stress-concentration factor from one of the Kt charts, like Peterson’s Stress Concentration Factors, is found. Finally, fatigue life is found using the fatigue curves (S-N curves) derived from the inputs with different fatigue loads and test materials.
Final thoughts
FEA Fatigue analysis makes the design and construction of components simpler and more manageable when done with accurate inputs and FEA experts’ help. They can help you understand the values, interpret results, and optimize the product for a flawless design.
Mechartes FEA Fatigue analysis experts can help you with accurate fatigue analysis and tests. With industry knowledge and experience of decades, Mechartes can use the right methods and techniques to produce the best outcomes for component design verification and optimizations.