FEA (Finite Element Analysis) has led to several advancements in engineering, enabling designers and engineers to develop enhanced structures and optimizations.
FEA Analysis is a computational technique that calculates the integrity and performance of structures using parameters and boundary conditions. Powerful computer processors and continuous software development have scaled the application of FEA analysis in the engineering field and medical and geospatial applications.
Although FEA has been used widely to optimize designs and increase their success rates, Failure FEA analysis has been used to determine the critical reasons for the failure of structures.
Structural failure can be attributed to several factors. Of course, some factors can be more evident than others. However, identifying the source of the failure is an essential feat that businesses often neglect, which can ultimately cost them the safety of the overall structure and can be heavy on their pockets.
Failure FEA analysis helps mitigate failures by identifying underlying risks and preventing danger from occurring.
What is Failure FEA Analysis?
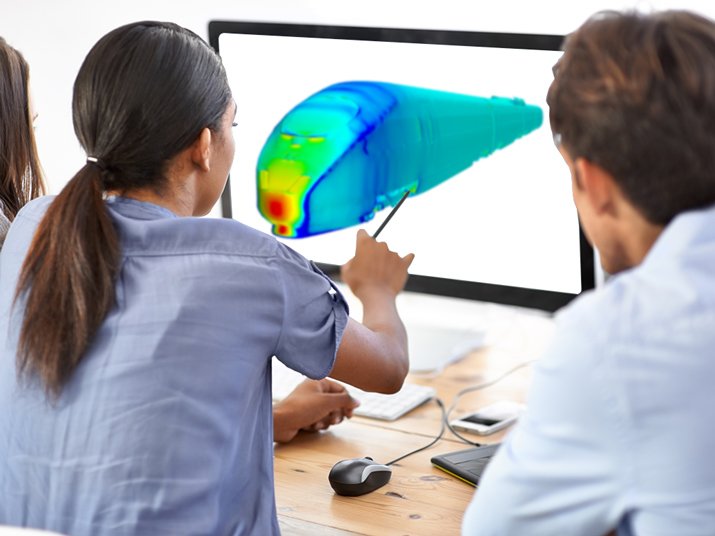
Finite Analysis is one of the most essential tools for design improvisations. The analysis includes creating a geometric model that consists of nodes and elements.
Software applications like ABAQUS and ANSYS are used to analyze failures and defects in the model and reconstruct possible sources of the failure.
The software generates images and animations that visualize the root cause of the failure. With progressive innovations to the FEA techniques and software applications, 3D models can be developed using advanced computer hardware.
Today, FEA calculations include a series of multiple physical environments and boundary conditions which dive deeper into failure analysis.
A general FEA method is performed in 3 phases:
-
In the pre-processing phase, the analyst creates a finite element mesh. Accurate data of the parameters or boundary conditions are added to the model.
-
The analyst then runs the governing mathematical equation of the model using a solver/solution program.
-
In the post-processing phase, the results produced are projected as visuals. Finally, these are evaluated and validated for further interpretation.
-
Based on the results attained, analysts can determine the failure points and the root causes based on the obtained data generated into a table or visual representations.
Failure FEA Analysis delivers quantitative and qualitative data about the causes of failure. Certain details and cues regarding the structure and failure mechanism may not be detected from visual examination or laboratory tests but can be easily observed from the results of FEA Analysis which can also support data obtained from these tests.
An accurate and reliable Failure FEA Analysis requires highly accurate data and a qualified FEA analyst with versatile knowledge of the techniques and niches.
A Failure FEA Analysis must be validated using experimental or real condition information further to guarantee the design’s success and enhanced integrity of the structure.
Read about Linear FEA Fatigue Analysis Here.
Instances of Failure FEA Analysis
Failure FEA Analysis can be used in several instances. Here are some case studies where Failure FEA Analysis was proven useful:
Failure FEA analysis – mechanical failure
Failure FEA Analysis was used to identify the stress distribution of a failed model of a 28MW horizontal hydro turbine shaft. The FEA Analysis was conducted under normal conditions and with various loads. The results correlated with fractography and metallographic observations.
Linear FEA Analysis was used to find out the stress state of the turbine shaft and shaft flange. ANSYS software was used for FEA modeling. Based on numerical calculations with two characteristic load cases, the crack initiation was at the shaft flange at maximum loads.
Several metallurgical and chemical composition tests indicated that the crack location was more susceptible to the high distribution of stress, which caused its failure.
FEA also revealed that the tensile strength on the shaft flange transition radius due to the loads was higher than recommended. This caused the increase in stress intensity factor in the crack tip to be higher than the material’s threshold.
It was also revealed that the shaft failure was caused due to corrosion fatigue which could have been avoided with adequate corrosion protection and periodic inspection due to the high stress on the delicate region.
Failure FEA analysis – corrosion failure
Another study was conducted by Karayan et al. on the failure of a seaware inlet pipe. A small leak was identified near a welded region near the backing bar.
Visual examinations and laboratory tests indicated cavitation with a crater-like appearance near the backing bar, which was an unusual appearance. Further FEA Analysis was used to determine the reason behind the cavitation.
Failure FEA Analysis was conducted with the pipe model and actual fluid conditions like velocity, temperature, pressure, and implicit parameters. FEA Analysis revealed that failure occurred around the location of the backing bar due to eddy currents.
FEA helped identify the root cause of the failure of the pipe, which was the location of the backing bar that caused eddy zones, leading to crater-like appearances, further leading to cavitation and a pipe leak.
Such case studies have indicated that although specific examination techniques can identify the location of the failure, Failure FEA can help understand the reason behind the failure and avoid similar occurrences in the future.
Build Failure-Proof Models with Mechartes
As mentioned earlier, Failure FEA Analysis is a sophisticated technique that involves expertise in mechanical engineering and its niches. It also involves accurate data to produce reliable results.
Mechartes’ validation services are experts in the various tools and software technologies involved in FEA Analysis. In addition, our engineering teams have worked on several projects to identify susceptible design problems and delicacies to help enhance the structural integrity and longevity of the model.
Mechartes Failure FEA Analysis services deliver highly accurate and reliable results to build sophisticated FEA models using available data. We use commercial software to analyze based on the geometric model and int boundary conditions involved to cater to your various business needs.
Reach out to us for validation services.