Computational fluid dynamics simulation, or CFD simulation, has been a game-changer in design, engineering, and testing scenarios. CFD simulation is a science that utilizes digital computers to produce quantitative projections of fluid flow about the conservation laws (momentum, mass, and energy) controlling fluid motion.
While this technology is used mutually in almost every area of design, testing, and engineering, we analyze ten crucial use cases of CFD simulation that have greatly benefited from the technology in recent times. Here, we look at ten crucial uses of CFD simulation and modeling.
Also read: How to Test Different Ventilation Strategies With CFD Simulations
10 CFD Simulation and Modeling Uses You Must Know About
The uses are as follows:
1. CFD simulation on HVAC applications
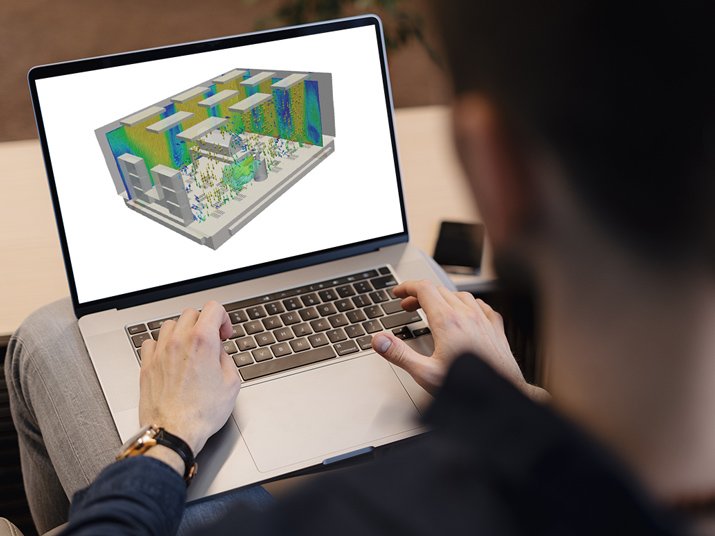
HVAC systems have become an integral part of our modern architecture. However, unlike past systems, expectations for today’s system are immense in every aspect.
Be its power consumption, capacity, effectiveness, operation time, and loss rate, today’s systems balance and ace every feature. However, since HVACs are custom designed and built to the unique needs of a venue, a lot can miss the mark.
CFD simulation technology is a godsend to designers and engineers who can now accurately model and test their designs without incurring significant financial expenses.
CFD simulations allow designers and engineers to fully build an environment and render the effects in real-time virtually. As a result, CFD simulations with HVAC systems provide an unbeatable edge in design and implementation, boosting efficiency and safety while being highly cost-effective.
2. Thermal management and heat transfer with CFD simulation
Speaking of HVAC, thermal management and heat transfer are two areas that can substantially benefit from CFD simulations. For example, thermal management is critical in server farms where temperatures vary greatly depending on the load and seasons.
CFD simulations help engineers understand this and set preventive management measures to ensure optimal performance of data centers.
Heat transfers are a tricky aspect unique to every situation and use case. CFD simulations allow engineers to build a virtual environment that’s 1:1 with the real thing and also serve as a reliable platform to conduct stress tests to ensure optimal heat dissipation and cooling.
3. Preventing cavitation using CFD simulation
Cavitation is the phenomenon where vapor bubbles are formed fortuitously within a liquid and interact with a metal object, causing damage.
For many years it was nearly impossible for engineers to test their prototypes for cavity damage as it occurs spontaneously and leaves the product damaged instantaneously.
However, with CFD simulations, testing and identifying this phenomenon has become possible. Digitally recreated designs are put virtually through various test scenarios to identify points of failure and make improvements to the product that can overcome them, making them more robust.
4. CFD simulation on high rheology materials
An area where CFD simulation techniques contribute irretrievably is with rheology materials (Solid materials that have the properties of a liquid when force or stress is applied directly to them):
-
Polymers
-
Plastics
-
Glass
CFD simulation techniques help manufacturers simplify their process flow and reduce energy and raw material wastage. It is the only method that can reliably help manufacturers plan their processes in fine detail.
5. Turbomachinery CFD simulation
The mechanical concept of turbomachinery describes the effect of energy generated by the compressing rotor that acts upon gas.
With various elements such as pressure, flow, and heat, CFD simulation is a purpose-built tool that can extensively simulate a design to help model, pre-process, mesh and optimize turbomachinery parts.
Also read: Why Are FEA Services Important for Engineering Industries?
6. Incompressible and compressible flow with CFD simulation
The most critical use case for CFD simulation would be simulating incompressible and compressible flow. Compressible fluid flow is a fluid flow where the density is not consistent like oxygen.
The incompressible flow would be liquid flow like water flow, as pressure does not impact its density. Both flow forms are a unique challenge for engineers and manufacturers and are an excellent use case for CFD simulation software. The simulation software is purpose-built to simulate the unique properties of liquids in a confined space.
7. CFD simulation for laminar and turbulent flow
While on the topic of flows, we can also attribute CFD simulations to being excellent at simulating laminar and turbulent flows of liquids with various properties in confined spaces.
CFD simulations help engineers and designers make decisions on inlets and outlets to reduce pressure and improve the efficiency of the flow. It also enables one-to-one simulation of any given liquid that provides us with an accurate representation of the real thing.
Also read: How CFD Simulation Services Can Improve HVAC Performance
8. Simulating aerodynamics with CFD
Aerodynamics is a highly complex field where CFD simulation technology contributes immensely. One can argue that aerodynamic computational requirements made way for modern computer-based simulation techniques.
Aerodynamics is significant in today’s designs, be it automobiles, aviation, or architecture. CFD simulations empower designers, engineers, and architects to design products that can take on challenges posed by aerodynamics at any scale. This process helps produce robust, aerodynamically compliant designs ready to take on any challenge.
9. Simulating reacting flows and combustion with CFD
Chemically reactive flowing fluids pose a substantial challenge for engineers as it is hard to envision and optimize during the research and design process.
However, CFD simulation technology has made it much more uncomplicated and accessible to design and test complex designs that deal with reacting flows. As a result, CFD simulation technology makes it safer, easier, and more cost-effective to build and test.
10. Battery simulation with CFD
The final and more recent noteworthy area where CFD simulations greatly benefit the industry is batteries. Unbeknownst to most, battery production is a multidisciplinary process that employs several engineering practices, including electrical, chemical, thermal, and fluidic engineering.
CFD simulations can provide many ways to design, test, and analyze battery designs and optimize their potency even before the design hits production.
With the rise in battery tech and more and more technologies being implemented precariously into them, R&D costs have ballooned to unimaginable heights in recent years.
CFD simulations can play a vital role in bringing down those costs and help us build a sustainable future quickly and effectively.
Concluding
CFD simulation technology has revolutionized design, engineering, and manufacturing across the board with its clear advantages. As our technology improves, we will see more and more areas where it can add more value to our collective future. There’s no question about the cruciality of CFD simulations, as it is now an integral part of our design process and here to stay.
Leading CFD companies specializing in optimal engineering and process designs can help solve complex engineering problems. With over 1500+ projects and 15 years of expertise, Mechartes is the premiere CFD company for CFD & FEA simulations and analysis consultation. Reach out today and kickstart your ideas into reality.