Computational Fluid Dynamics (CFD) is frequently used in architectural design to simulate airflow and temperature in interior spaces. This enables designers to examine interior conditions before a structure is constructed, allowing them to try many possibilities and choose the best ones.
CFD can be used for modeling:
-
Thermal management and heat regulation are based on occupants’ requirements.
-
Conditions within a space based on the existing environmental factors
-
The performance of cooling and heating elements in the building, such as the positioning of air inlets and extracts or radiators
-
Elements and factors that contribute to higher fire risks and damage.
-
The performance of natural ventilation and the placement of vents, windows, and doors
-
Heat accumulation in high heating rooms such as kitchens, server rooms in data centers, etc.
-
The placement of sensors and fire extinguishing showers
Typically, simulations are conducted for various scenarios, evaluating behavior under various occupancy levels, climatic conditions, modes of operation for building services, openings between areas, and so forth. This helps to give a detailed visualisation of how a structure will probably react under typical operating settings and exceptional or extreme circumstances.
Core Components of CFD Analysis
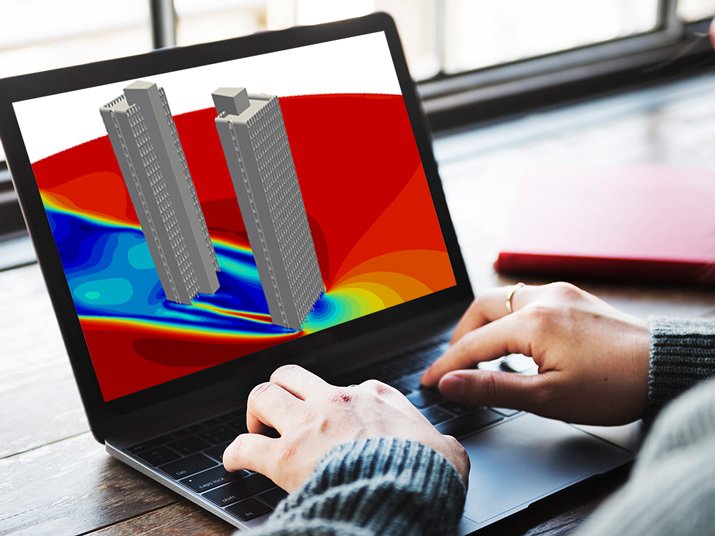
CFD allows engineers to examine the impact of fluid flow on their designs. Mathematical concepts like partial differential equations (PDE) and Navier-Stokes are automated and solved using CFD. CFD analysis for building design optimization and validation takes place in 3 phases.
Here is a quick overview of each of the phases in CFD analysis used to
Pre-Processing
The initial phase in a CFD simulation is pre-processing, which, if done correctly, can precisely define the simulation’s parameters.
This stage entails identifying the area of interest, breaking it into manageable segments, setting the boundary layer and conditions, meshing the geometry, and determining the materials’ characteristics.
In the pre-processing stage, there are some essential steps that CFD experts perform before moving to the processing phase.
Important Pre-Processing Elements
The quality of a CFD analysis depends on how well the model is built. It is imperative that the designer check the geometric model for flaws or inaccuracies. Some common problems include:
-
Deficits in the model
-
Overlapping or absent faces
-
Unclosed geometries such as vertices, free faces, and edges
The model should be a “closed” solid after preparation, free of the aforementioned mistakes.
Problem Analysis
The foundation of any simulation is problem analysis; to establish your purpose and parameters correctly, you must aggregate the issues you are trying to address.
Find answers to relevant questions like are you attempting to understand the mechanics of the problem? For example, do you wish to understand the laminar and turbulent blood flow through the veins as it responds to a pressure change? Or are you assessing how well a new kitchen appliance design transfers heat?
You will be able to define your model with the proper properties and avoid using inaccurate data in your simulation results by performing a thorough problem analysis.
Geometry
After your physics is established, you must design a two or three-dimensional geometry based on the findings of the issue analysis.
Some issues may be resolved in two dimensions, which can speed up calculation and save money. GAMBIT and Design Modeler, are programs more suited for two-dimensional requirements. For three-dimensional models, programs like Autodesk Inventor, Spaceclaim, CATIA, Solidworks, or Design Modeler will be more appropriate.
Meshing
Meshing needs to be done carefully. If done incorrectly, it might have a cascade effect on your study. This stage entails dividing your model into predefined areas known as cells or control volumes.
The fluid flow equations that regulate these cells further describe them, therefore the designer must make an informed decision regarding the flow profiles of these cells.
Most designers discover that minimizing the size of these cells can help you guarantee precision throughout the analysis.
Solver Configuration
The conditions of the problems you intend to solve must be defined at this stage. For instance, boundary conditions, fluid type, turbulence model, stationary or multiphase flow, and transient one-phase.
The physics of the problem must be understood as the numerical solutions are pre-configured. You also need to understand how the technique functions. You can decide which processors to employ during processing and how many iterations are required to reach convergence.
Results
Validating your setup is the final component of pre-processing. You can do this by looking at experimental or analytic data.
Processing
Each simulation procedure utilizing a CFD application must adhere to a predetermined set of procedures. Simulations include a set of instructions that must be followed in order to prevent being stuck or obtaining error messages in later phases. Each of these procedures depends on the others, which is why effective pre-processing is so important.
Post-Processing
Your next step is to analyze the findings you obtained from the simulation stage. To do this, make use of the tools at your disposals, such as vector plots, contour plots, data curves, and streamlines.
You will receive accurate information and graphical representations in this step. EnsSight, ANSYS CFD-POST, ParaView, FieldView, and Tecplot 360 are a few of the well-known software programs utilized in the post-processing step. This phase’s procedures have the following tasks:
-
Obtained quantities are calculated
-
Determining parameters
-
Visualization
-
Analyzing data systematically, debugging, checking, and validating the CFD model
Mechartes CFD Analysis Services for Building Design
A key portion of performing CFD analysis is having the expertise and knowledge to feed the available data into relevant software programs to yield accurate results. Without adequate expertise, CFD simulation can result in faulty results and model performance validation.
Mechartes offers CFD Analysis services that enable building designers and architects to gain accurate insights to enhance and optimize their designs. Our expertise and industry knowledge helps us apply the required data to the CFD software to produce reliable and efficient results to maximize ROI on building design.