Computational Fluid Dynamics (CFD) analysis can be an engineer’s best friend or worst nightmare. Engineers who understand the process’s basics and complexities will find it a versatile tool. However, everyone faces issues in CFD analysis at some point or another. Read about the common roadblocks of CFD analysis and ways to overcome them to achieve accurate results.
What is CFD Analysis?
CFD analysis helps understand fluid flow in and around structures for static and dynamic conditions. Different boundary conditions are set according to specific project requirements for the CFD analysis, and the engineers then study their results. The analysis is run again if a need for modification arises; otherwise, the result is declared final and fit for proceeding.
How is CFD Analysis Helpful?
Applying different conditions to run the stimulation helps better understand the structure’s strength and helps avoid severe structural problems later on. CFD is also useful when experimenting with the design model and theoretical conditions to understand the real-life possibilities of an idea or theory.
Common Roadblocks for CFD
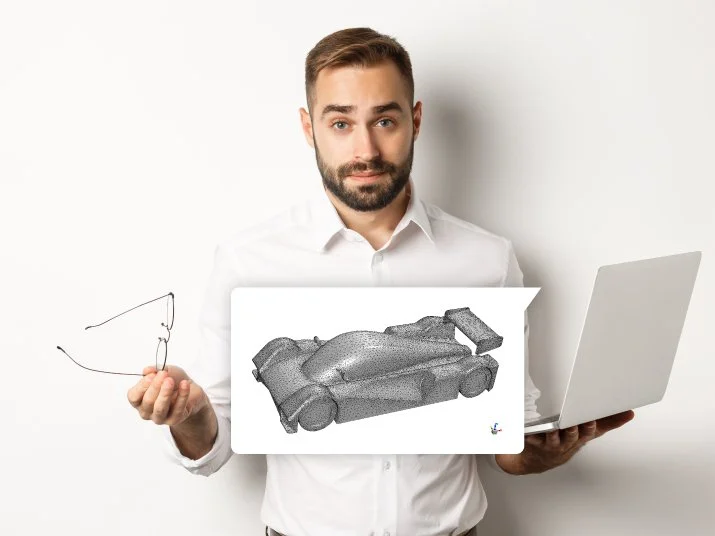
While CFD analysis is quite streamlined, some conditions can pose significant roadblocks. These are not very severe obstacles and, once understood, will not create a problem. Some of the most common roadblocks for CFD are:
1. Size of the Mesh
This is a very common mistake made while running a CFD analysis. The size of the mesh creates a big impact on the precision of the result. While Finite Element Analysis (FEA) is comparatively easier to perform with a big mesh size, CFD analysis requires a very small mesh size. The small mesh size ensures accuracy in working out the analysis evenly and correctly under different conditions and instances. A CFD analysis can take hours or days to complete.
2. Trouble Due to Turbulence
Turbulence is yet another common hurdle for CFD simulations. The turbulent flow arises due to three-dimensional fluid flow in space and time. This minimizes the distance between the discrete points and ultimately affects the time taken for the analysis.
3. Solution Convergence
The convergence in the solution graphs might occur due to multiple reasons starting from the structure’s geometry, mesh size, calculations, or boundary conditions. Some users painstakingly locate the problem and then resolve it, which makes it a time-consuming problem.
Surpassing the Roadblocks
The issues in CFD analysis are not as big as they seem. Let us understand how to resolve the three roadblocks mentioned above:
1. Decrease the mesh size
As the analysis needs to be accurate, always remember to increase the number of mesh blocks and decrease their size as much as possible. This enhances the application of conditions evenly throughout the design model.
2. Turbulence Treatment
Several models are designed to tackle the turbulence problem by giving an equation between energy dissipation and viscous flow. These models vary with changing conditions, and using these models interchangeably can prove disastrous.
3. Pay Attention to the Conditions
The only way to avoid convergence in the solution graphs is by paying attention to the input values and checking the conditions and calculations at every step. The engineer must pay extra attention while entering the details into the software and spot any irregularities.
Frequently Asked Questions
1. Is mastering CFD analysis essential for design engineers too?
No, it’s not. If your main focus is ideation design and you are not a part of the production team, then there is no need to learn CFD analysis. However, if you grasp it, your designs will have an extra edge as they are more practical, accurate, and manufacturing ready.
2. How much time does it take to learn CFD analysis?
About 4-6 months. However, the duration needed to learn software depends on how proficient they want to be. Learning to simulate machine parts will take lesser time when compared to simulating whole buildings.
3. Can I get professional help with my CFD analysis?
Yes, companies like Mechartes can help you with CFD analysis. They have a team of trained professionals who are efficient in CFD analysis and can help you understand and run simulations accurately.
Ready To Go Ahead?
We hope it will be easier to deal with roadblocks during your CFD analysis. Mechartes has an army of professionals with years of experience ready to assist you with CFD analysis of designs related to the oil and gas fields, water treatment, and heating, ventilation, and air conditioning (HVAC). Visit our website for more information and further assistance.