Computational fluid dynamics (CFD) mainly involves the numerical analysis of fluid flow patterns. It is used to study the interactions between fluid-fluid, fluid-solid, and fluid-gas systems and has wide applications in the fields of aero and hydrodynamics. Moreover, it enables simultaneous measurement of several desired quantities at high space-time resolution. Mechartés uses computational fluid dynamics for modeling parameters like temperature, humidity, thermal radiation, and air velocities which control the thermal environment inside buildings.
Any construction’s structural integrity and design are crucial for its long-term sustenance. Optimum cooling and air circulation play a vital role in the smooth functioning of a structure. At Mechartés, we model and design ventilation systems for buildings like airports, malls, museums, auditoriums, and basement parking spaces to optimize the facility’s cooling and air distribution system.
We also undertake projects involving performance analysis of a computer room air conditioning with detailed rack-by-rack inlet and exit temperatures and 3D thermal mapping of data centers. The results from our simulation can identify recirculation areas between the units. In addition to cyber safety, a data center’s structural competence and design are crucial for its long-term functioning. So, IT firms, web hosting, and cloud service companies spend big bucks on the security and maintenance of these facilities, which act as storehouses for maintaining computers and their auxiliary systems.
Optimizing heating, ventilation, and air conditioning are essential in ensuring any construction’s long-term, uninterrupted functioning. Our team of dedicated and skilled engineers uses computational fluid dynamic analysis to predict airflow patterns inside enclosed structures and spaces. We take on projects which involve reconfiguring existing facilities and designing new ones. Read on to find out how we go about achieving our goals.
The Computational Fluid Dynamics Process
Computational Fluid Dynamics consists of three basic steps:
1. Pre-processing
This step makes assumptions to model the flow type, and the presented theoretical problem is converted into a mathematical and numerical computer model. In addition, pre-processing also involves the generation of meshes and the application of boundary conditions.
2. Solving
The solving phase involves harnessing the computational power. Here, the solver performs actual computations. The outcome of this step is enhanced using multiple solvers with variable efficiency and capability.
3. Post-processing
In the post-processing step, an analyst visualizes, analyzes, and verifies the results. The analyst draws conclusions based on these results, which are finally presented with the help of graphs, motion pictures, and tables.
Types of Meshes Used in Computational Fluid Dynamics
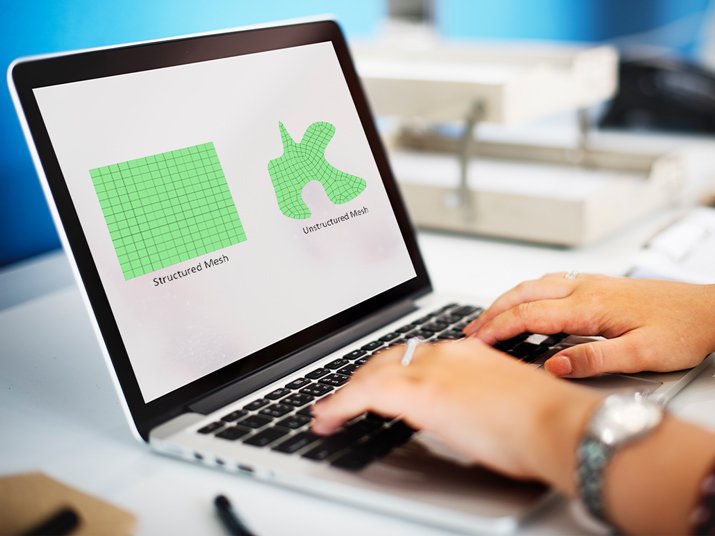
A mesh consists of a set of points and cells that connect to form a network of variable geometry, topology, and size. They are widely used to solve partial differential equations. Each cell of the network holds the solution to the equation, and combining the outcome from multiple cells in the network provides the solution for the entire mesh. Primarily, computational fluid dynamic studies have two types of meshes, namely, structured and unstructured.
Structured Mesh
A structured mesh is also known as a grid. Identifying adjacent cells and points on a structured mesh is effortless because of their layout and formation. They are applied extensively over coordinate systems with definite geometries like rectangular, elliptical, spherical, and others. The numbering of the cells in the structured mesh follows a pattern that allows adjacent cells to be queried based on their coordinates, which proves beneficial from the programming aspect.
Unstructured Mesh
Generally, the decryption of complex geometries uses unstructured meshes, which cannot be analyzed using ordered structural meshes. Their flexible nature supports the coexistence of multiple cell types within the same mesh, improving the geometry fitting and the element quality. The distribution of points along the complex geometric surface is determined using the meshing algorithm. Additionally, the algorithm governs the connection patterns between different surfaces and the number of points required to create a curve on the surface. Surface geometries that fall outside the specifications of a structured mesh are tricky to handle. In such cases, the discretion of a flow solver comes into play.
Combining Structured and Unstructured Meshes in Computation Fluid Dynamic Analysis
Flow solvers at Mechartés use a combination of structured and unstructured grids to study the dynamic optimization of the thermal environment and provide adequate cooling solutions. The engineers use their expertise to switch between meshing techniques depending on the intrinsic nature of the geometry component of the surface under question.
They employ computational fluid dynamic codes to model and analyze the cooling effectiveness between the nooks and crannies of the building. Our team uses software solutions to design a graphical user interface that allows positioning, sizing, and characterizing spaces in plan view.
Following this, they model airflow and temperature distribution in the facilities, which involves obtaining thermal profiles. The focus is identifying potential high-temperature zones within the architecture and performing 3D thermal mapping to understand how cold air moves through the entire area.
We also focus on the performance analysis of heating, ventilation, and air conditioning systems that consume far more energy than required. In addition, we also carry out detailed inlet and exit temperature mapping. Our computational fluid dynamic models are based on thermal mass and energy balance principles. We conduct complex studies to predict accurate airflow analysis to reduce air contamination while also improving numerous facilities’ energy efficiency.
The Takeaway
The results from our simulation are used to identify recirculation areas and provide a detailed 3D analysis of the movement of cold air inside the building. In addition, the simulations provide the performance analysis of heating, ventilation, and air conditioning systems while studying the facility’s inlet and exit temperatures and 3D thermal mapping, highlighting trouble areas. Our models can evaluate the airflow rates and thermal loads to optimize energy consumption.
Mechartés undertakes projects which involve reconfiguring existing facilities and designing new ones. So, feel free to contact our service advisor for more details.