Heating, ventilation, and air conditioning (HVAC) systems are widely utilized to manage the air change rates per hour inside buildings and contribute to significant energy consumption. HVAC systems account for 60% of the total energy consumption of buildings.
Hence, it is essential to develop better control techniques for HVAC systems to provide occupancy-driven energy and comfort management due to the significance of building energy conservation.
Simulation studies are commonly used in the construction, aerospace, and automobile sector. Overall, simulation technology, coupled with CFD analysis, helps tap into this technology’s fullest potential, allowing engineers and architects alike to predict and optimize the performance of the buildings in their early stages of development and enhance the design process. HVAC simulations are used to validate and predict wind loads on the system. Further, CFD and simulation studies optimize buildings for thermal comfort. Accurate analysis of airflow aids in controlling air contamination and improving the quality of air.
By using simulation studies coupled with appropriate CFD solutions, significant amounts of energy can be saved, increasing the energy efficiency of HVAC systems in buildings that consume way more energy than required. CFD analysis and ventilation simulations can help you improve your ventilation system design by reducing the pressure drop and optimizing air flow. They are used for understanding air flow, heat, cooling effects, water pressure, wind analysis, and heat production due to anthropogenic activities in and around the structures.
These tools have been used extensively in designing automotive HVAC systems to optimize system performance and shorten product development time. They offer a better insight into the flow characteristics of the HVAC systems.
How CFD Analysis Aids in Improving HVAC Systems?
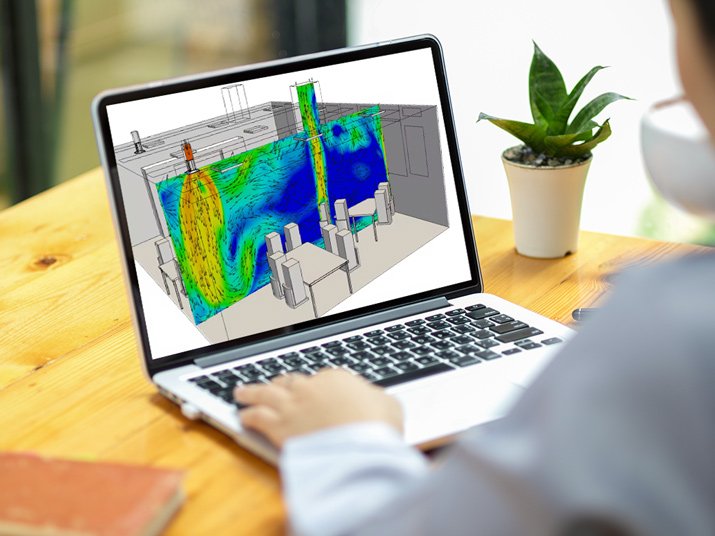
Early analysis of HVAC systems did not espouse the use of CFD, instead relying on numerical methods to provide guidance for the enhancement of the design and functionality of HVAC systems. More recently, CFD analysis has become vital to design engineers, and researchers are interested in obtaining fast and accurate data to make informed HVAC technology design decisions.
CFD is an optimum tool for analyzing three-dimensional airflow for large indoor spaces, which are otherwise difficult to be modeled using a network of one-dimensional flows. Evaluating the indoor air environment is the main target of CFD analysis for designing and testing ventilation systems.
Testing Ventilation Performance
CFD-based ventilation test methods involve integrating a conditioned room model into its ventilation system and control strategy to evaluate ventilation performance. The test method is feasible to investigate ventilation control performance in a simulated environment as an evaluation tool for ventilation systems and control strategies.
When applying CFD to HVAC systems, the two significant components indispensable for indoor ventilation performance tests include the simulated ventilation room and the ventilation control system. Both of these are essential tools for analyzing indoor environments and space ventilation.
The CFD model provides the alternative for representing the room as a virtual ventilated model. A proper numerical model for CFD simulation is necessary to obtain accurate data. The computational accuracy of the analysis can be significantly improved by adopting a reasonable numerical model.
Testing Thermal Performance
CFD analysis allows measurement of the thermal performance of the HVAC module through user-supplied subroutines, which model the thermal effects of heat exchangers. CFD techniques can predict the HVAC performance in different operating environments.
Complex indoor thermal conditions, especially the temperature difference between the actual sensor location and the occupied zone, are compensated using space temperature offset models.
Mesh Generation and Boundary Conditions
One of the largest sources of error in CFD modeling of HVAC systems occurs while defining realistic boundary conditions. Commercial CFD codes are good for engineering purposes when appropriate grids and numerical schemes are used.
Problem areas from the flow results are identified and resolved using variable mesh geometries and boundary conditions. With the advent of advanced commercial solvers, improved auto-meshes, and high-performance workstations over the past few years, the application of CFD in testing the design stages of automotive HVAC systems has increased numerously.
Uniform velocity and pressure boundaries are often applied at the inlet and outlet boundaries in these analyses. These boundary definitions usually account for many errors in the CFD analysis.
Assembling Components of a HVAC System in a CFD model
Much work has been done on the components of a HVAC system, such as the plenum, HVAC module, fan blower, inlet, and air distribution ducts. Until recently, individual HVAC components have been modeled separately.
Assembling the variable components of an HVAC system and analyze them as a complete unit eliminates many of the errors generated by unrealistic boundary assumptions, thus resulting in a more accurate solution. Modeling the entire system, as opposed to individual components, eliminates many of the mistakes associated with boundary conditions, increasing the validity of results.
Ventilation Simulations for Improving Performance of HVAC Systems
Two separate simulations with different degrees of modeling are carried out simultaneously to study the macroscopic features of flow transport of HVAC systems inside buildings. The space distribution features in each room are analyzed with respect to the flow transport of the entire building. The modeling degrees, such as accuracy, reliability, and model coverage, should depend on the engineer’s requirements.
The engineer measures the airflow supply velocity and compares the obtained figures with the numerical results to ensure that the spacing between the heat transfer devices is varied to optimize the performance of HVAC systems. They carry out the experimental measurement to validate the numerical models and to obtain the required initial and boundary conditions. A combination of single and spot cooling strategies gives optimum cooling and ventilation results. The combination cooling strategy aims to obtain maximum cooling efficiency with the minimum number of nozzles and total airflow.
At Mechartés, we perform CFD analysis and ventilation simulations to optimize the energy consumption of HVAC systems. These methods help our engineers expeditiously evaluate the flow fields for several design variations in a relatively short amount of time. Our cutting-edge solutions adequately capture the relevant physics while offering cost-saving attributes by conserving and optimizing the energy consumption for HVAC systems in variable environments and facilities.
The Takeaway
The results from our ventilation simulation studies are used to identify recirculation areas and provide a detailed 3D analysis of the movement and build-up of stagnant air pockets within the airflow of indoor spaces. In addition, the simulations provide the performance analysis of HVAC systems while highlighting areas that lack recirculation. Our CFD models can evaluate the airflow rates and optimize the energy consumption of HVAC systems inside buildings and other complexes.
Mechartés undertakes projects which involve reconfiguring HVAC systems for existing facilities and designing new ones. So, feel free to contact our service advisor for more details.