
Buffer Tank Simulation
At Mechartés , we’ve been pushing the boundaries of building and infrastructure design for 16 years, working on complex projects across the Middle East and globally.
One of our specialties is designing Thermal Energy Storage (TES) tanks, which play a crucial role in reducing operating costs and increasing efficiency in HVAC systems.
In this article, we are sharing a case study on how we used Computational Fluid Dynamics (CFD) and Finite Element Analysis (FEA) to design a TES tank for a client. Our goal was to create a tank that effectively stores and releases thermal energy, minimizing de-stratification and maximizing efficiency.
1. The Challenge of TES Tank Design
Thermal Energy Storage (TES) systems play a crucial role in storing thermal energy for later use when it’s more cost-effective or necessary to generate energy. By utilizing TES tanks, the operating costs and required capacity of cooling and heating plants are significantly reduced, leading to increased efficiency and lower capital costs.
Designing TES tanks requires a meticulous approach to ensure they effectively store and release thermal energy as needed for various applications, including HVAC systems, renewable energy integration, and industrial processes.
At Mechartes, we specialize in guiding clients through the comprehensive design process, covering all aspects of TES tank design, including mechanical, process, and structural considerations.
The thermal stratification within a TES tank has a major impact on the thermal performance of HVAC chiller systems. To avoid de-stratification, it’s essential to prevent water jets from entering the tank. Typically, TES tank inlets and outlets are designed using octagonal slotted pipe type or radial disk type diffusers, which effectively prevent de-stratification and promote optimal stratification within the tank.
2. Our Approach and CFD Analysis:
Our objective was to carry out mechanical and structural design for the TES tank, including designing the internals and the tank itself.
As part of the project scope, we designed and validated radial disc diffusers using transient CFD analysis for both charging and discharging modes of operation. This analysis demonstrated the thermal stratification inside the TES tank and showed that well-designed TES tank diffusers can deliver a Figure of Merit (FOM) of 85% to 90% as recommended in ASHRAE standards. We followed the guidelines from the 2020 ASHRAE Handbook—HVAC Systems and Equipment, Chapter 50 on Thermal Storage.

TES Tank Model
3. Structural Design:
For the structural design, we performed calculations for the shell and roof plate thickness, central column, bottom plate, annular plate, stiffener ring, and other components.
In summary, the structural design calculations included:
-
Shell and roof plate thickness calculation
-
Central column calculation and structural member requirement fixed cone roof
-
Bottom plate and annular plate calculation
-
Stiffener ring calculation
-
Requirement for nozzles as per EN standards.
-
Anchorage calculation and Anchor chair calculation
-
Structural calculations for internal pipes and diffusers
-
Structural calculations for Stairs and platforms.
For structural integrity, we adhered to EN-144-15-2205 standards, ensuring robust construction using appropriate materials for the tank’s shell, roof, bottom plate, annular plate, structural members, compression ring, stiffeners, stairs, and platforms.
4. Conclusion
4.1. CFD Analysis:
We designed radial disc diffusers for the TES tank based on input parameters, considering the limiting values of Froude Number, Reynolds number, and other considerations. We also considered the design flow rate during the discharging mode and charging mode for designing the TES tank diffuser system. The TES tank diffuser system was designed with radial disc diffusers located at the top and bottom to enable the distribution of incoming flow to the complete diameter of the tank.
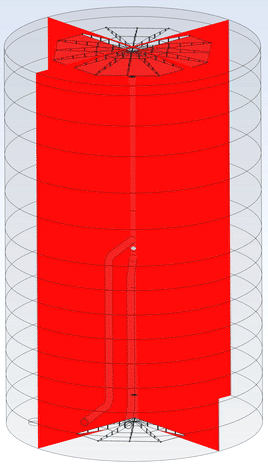
TES Tank Temperature Animation
To maintain low velocities from the diffuser piping, we selected the central pipe and branch pipes connected to the top and bottom diffusers to limit the maximum velocity entering the diffuser from the pipe to be less than 1 m/s. We carried out a series of small-scale CFD analyses to achieve the lowest possible velocity (or Re) with close to uniform velocity distribution at the outlet of the diffuser for the given tank size and maximum design flow rate condition.
Based on the small-scale results, we selected an appropriate design and carried out a full-scale transient CFD analysis for both charging and discharging modes for the operation duration. The CFD results of velocity and temperature profiles inside the tank, along with thermocline thickness results and FOM, were presented from the full-scale CFD analysis.
4.2. Structural Calculation
1. Hot water thermal energy storage tank is designed as per guidelines given in standard EN-144-15-2205.
2. Material used for construction of shell, roof, bottom plate, bottom annular plate, roof structural members, compression ring, stiffeners, stairs and platform structural material etc. were provided.
3. Fabrication drawings for tank construction were provided.
Final Note
At Mechartés , our expertise in CFD and numerical analysis enables us to provide clients with actionable insights and recommendations, empowering them to make informed decisions about their designs.
We are dedicated to delivering accurate simulation results and professional engineering services, driven by our team of young, talented engineers who work collaboratively to ensure that every project receives the attention and expertise it deserves.
If you have any comments or observations on this whitepaper, please don’t hesitate to drop me a note at srihari@mechartes.com.