1. Objective
The objective of the analysis is to study pressure variation and induced stress (as per API 674) for the reciprocating pump system.
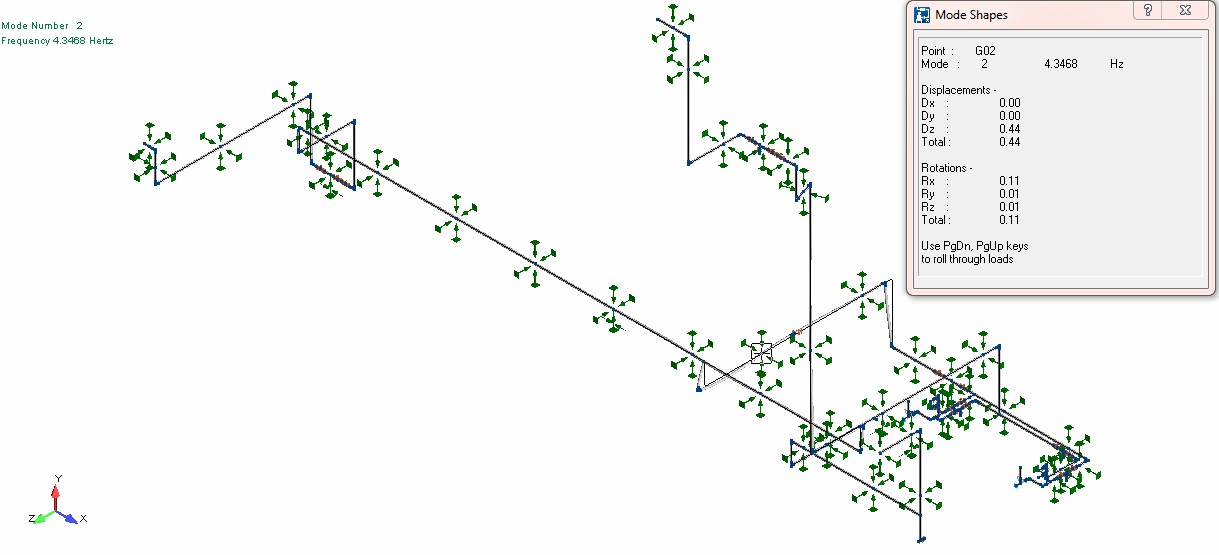
-
To study the mechanisms of the starting point in the development of practical methods for the analysis of the vibro-acoustic behavior of fluid filled pipe systems.
-
To be able to solve the reliability and noise problems, which will be of great importance to understand the mechanisms that are responsible for the generation and the propagation of fluid pulsations.
-
To control detrimental pulsation and vibrations, the API standard 674, third edition, mentions two design approaches. The first design approach involves pulsation and vibration control. The second approach involves pulsation control through the use of pulsation control devices developed using proven acoustical simulation techniques in conjunction with mechanical analysis of pipe runs and support system to achieve control of vibration response.
-
Determination of network Natural frequencies.
2. Design Approach
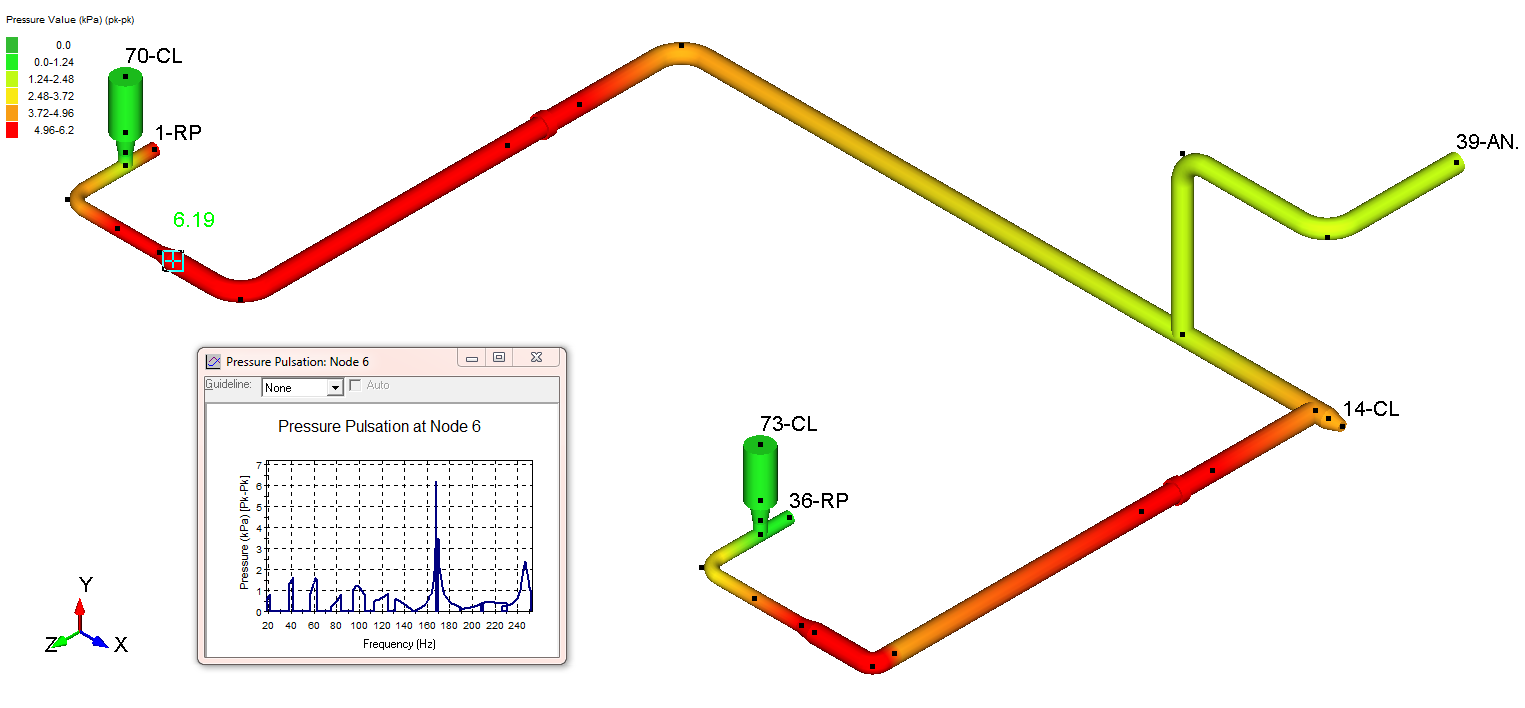
PULS employs an efficient transfer matrix approach and assumes a steady pulsating flow condition that will not die-out over time.
PULS also assume one dimensional plane wave theory. The plane wave theory assumption holds for frequencies where the wavelength is larger than twice the pipe diameter.
This assumption holds well for most gas systems below 200 Hz. For liquid systems and systems with small pipe diameters, the plane wave theory can be applied for frequencies of 500 Hz or more.
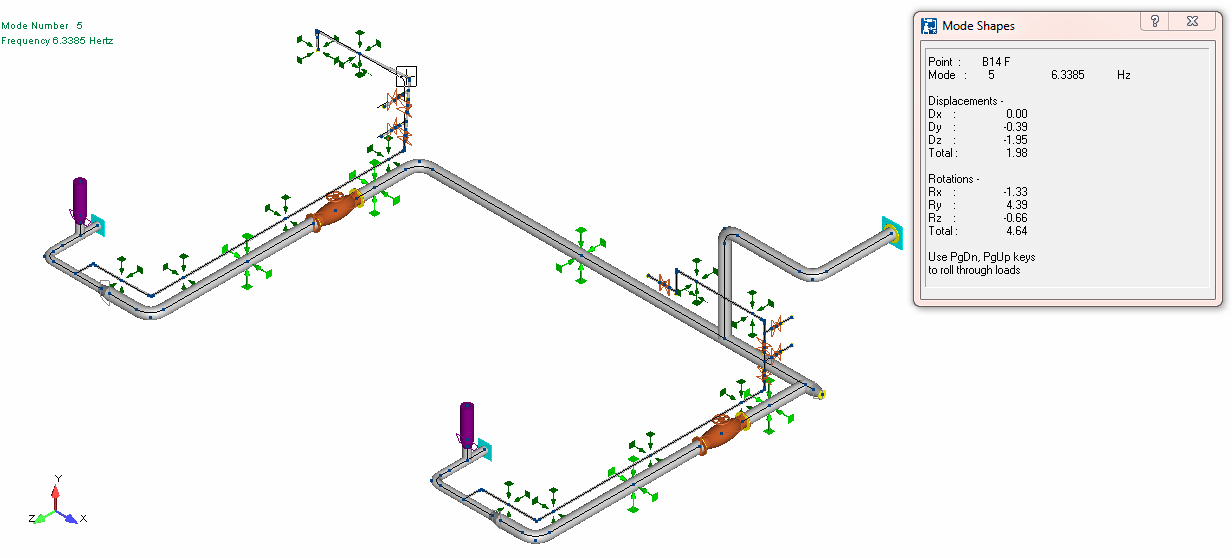
Suction Pipeline: The fluid at suction side of pump is provided by the water injection tank. Pipes connected to pumps are 4 inches while pipes connected to tank are 6 inches. The pumps are septuplex, reciprocating and plunger type.
Discharge Pipeline: The discharge line provides fluid to heat high separation air cooler. Pipes connected to these pumps are 4 inches.
3. Conclusion
Results obtained from pulsation analysis of suction and discharge lines show pulsation peaks which are lower than the allowable values as per API 674.
Bladder type pulsation dampener of 6L capacity along with an orifice plate of beta ratio 0.45 play an important role in controlling the pulsation level in piping network. The pressure drop through the orifice plate is 204.3 kPa and is placed downstream to pulsation dampener. The location of the orifice plate is marked in the drawing provided with this report.
Also, it can be seen from the results obtained from mechanical vibration analysis of complete piping system that the pipe stresses for harmonic forces are under allowable limits. Some supports are modified, and few supports are added in both suction and discharge piping network.