-
To demonstrate that the proposed design of the separator will meet the performance specifications specified by the end user for both the maximum gas flow rate and maximum liquid flow rate Design Case process conditions.
-
CFD studies are used to analyze the velocity distribution of the gas and liquid phases inside the Separator to verify that the velocities stay within the acceptable design criteria requirements of the end client.
-
In addition, the CFD analysis will predict the droplet cut-off size to verify whether or not CFD Analysis achieves the droplet cut-off size requirement.
2. Modelling & Meshing
From the geometries, hybrid meshes were created using a combination of tetrahedral, polyhedral, and hexahedral elements. The mesh was optimized to be grid-independent, allowing the CFD simulation results to be independent of the mesh size and shape.
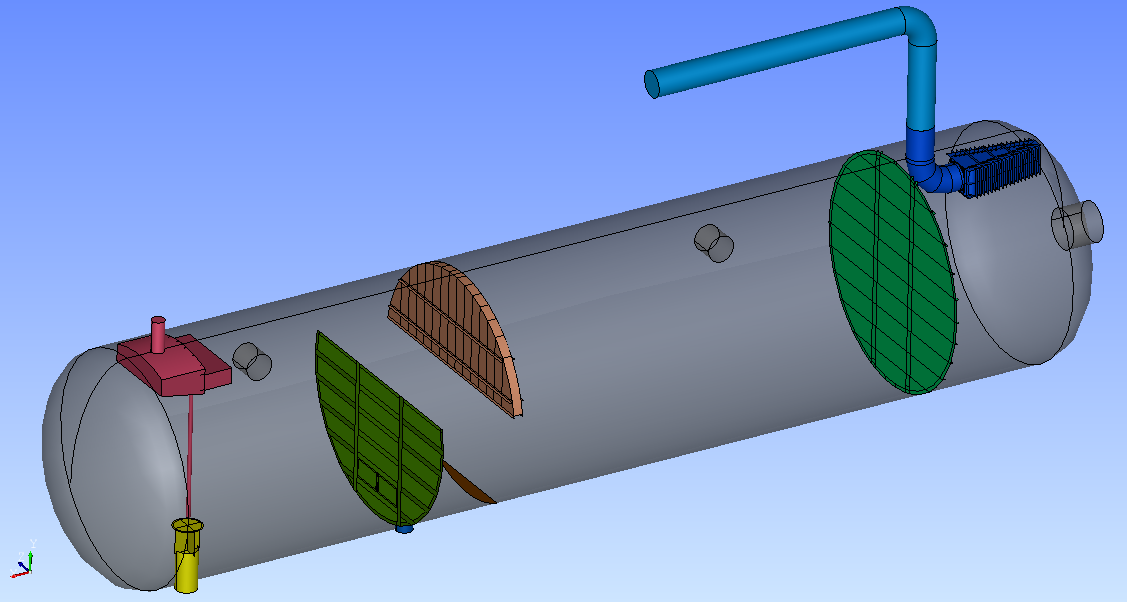
The meshes were optimized at this level of discretization points to provide a stable numerical solution within a reasonable calculation time.
At this level of discretization points, the CFD simulation results will not change significantly with further increases in discretization points; i.e., the meshes can be grid-independent.
3. Design Approach of 2 Phase CFD Analysis
The Population Balance Model (PBM) model simulations have been initiated using a developed flow resulting from simulations with the Eulerian-Eulerian model, aiming for more rapid convergence of the solution and optimize separation efficiency. The inlet was applied to the fluid flow rate and fluid properties of phases. It is required to check the possibility of phase inversion at the inlet. Therefore, a pipe length of 6m upstream has been modeled as per actual Pressure drops across perforated baffle plates, and foam breakers are modeled using a porous formulation. The perforated baffle plates then redirect the fluids into the gravity separation zone.
4. Geometrical Parameters of 2 Phase CFD Analysis
The CFD analysis considered crucial geometrical parameters of the separator, including the dimensions of the inlet and outlet pipes, the placement and configuration of internal elements like baffles and foam breakers, and the overall shape of the vessel. These factors significantly impact flow patterns and separation efficiency.
5. Conclusion of 2 Phase Separator CFD Analysis
A detailed 2 Phase Separator CFD Analysis was carried out, and it concluded from the detailed analysis that a clear and effective separation of liquid and gaseous phases is observed throughout the inlet pipe. Maximum water in oil (WIO) is calculated at 2.3% v/v, most water droplets in liquid HC are greater than 100 microns, and maximum oil in water (OIW) is calculated at 243 ppmw. Time-averaged liquid carryover at the gas outlet is calculated as less than the 0.132 USG/MMSCF.